In this post, we will show you some advanced energy saving technology in air compressor for your reference.
Two-stage compression technology
Two-stage compressor(or Dual-stage compressor) energy-saving 5%~13% over equivalent sized single-stage compressors. But why?
– Adopt two-stage compression to attain reasonable pressure distribution and reduce each compression ratio, which can achieve the compressor’s power savings.
In a single-stage compressor operating at 100 PSIG at sea level, the compression ratio is 7.9 to 1 (in absolute terms). But a two-stage compressor operating at the same pressure will have a compression ratio of 2.8 to 1 in each stage (2.8 is the square root of 7.9) .
– Low compression ratio reduces the internal leakage and improve volumetric efficiency.
– Low compression ratio reduces the bearing load, improve the bearing life and extend the life of the host.
30~40bar two-stage compression energy saving air compressor
for PET bottle blowing, aerospace plants
5~10bar oil-lubricated two-stage compression energy efficient air compressor
for Chemical, Mining, Electricity, Power plants, Cement, Glass blowing, Spinning, Textile
7~10bar 100% oil-free two-stage compression most energy efficient air compressor
for Electronic, Food, Pharmaceuticals, Chemical and so on.
Oil-free Technology
Oil-free technology reduces expenditures in these ways:
– Saving energy due to hot air discharge
The superior cooling capability of lubricating water ensures that the heat is removed efficiently at the source gives more air per kW of power. The operation temperature is about 55℃, there is no need to be cooled and discharged directly.
– Saving the costs of extra energy to combat pressure drop due to oil air separation unit.
For the oil-lubricated screw air compressor, the oil air separation unit resistance leads to pressure loss. Power consumption increases by 0.3%~0.5% for every increase of pressure drop of 0.1bar
– High compression efficiency due to low temperature ideal isothermal compression
For the oil-lubricated screw air compressor, high Interstage and exhaust temperature, rise every 10 ℃, power consumption will increase 3% as a result.
– Cutting maintenance costs and treating oily condensate costs
Avoiding expensive oil, oil-filter, air oil separator, oil cooler costs.
Low temperature reduces the stress on components ensuring long life.
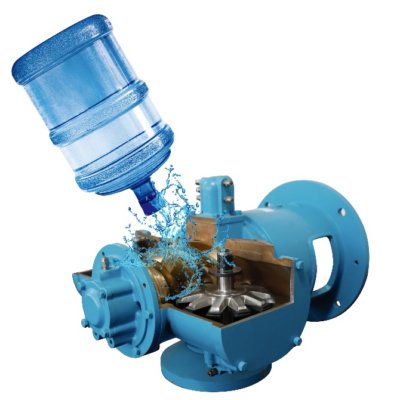
Water-lubricated oil-free energy saving series air compressor
Variable Speed Drive (VSD) Technology
You may doubt that the initial investment of the VSD screw air compressor is higher than the Fixed speed one. Should I Buy a VSD Screw Air Compressor?
– Why does Variable Speed Drive (VSD) save energy when compared to fixed speed?
- Compare it to a car, fixed speed is either drives 100 km per hour or not at all. Fixed speed compressors run at one fixed speed, and are very efficient when operating fully on load 100%, but most applications don’t, they have a fluctuating air demand.
- Variable speed drive (VSD) compressor can adjust its motor and elements speed to match the air demand, which saves considerable amounts of energy.
- Generally, use VSD can save 10% ~ 35% energy, it depends on the working conditions of the air compressor. When the customer’s air consumption fluctuates greatly, the energy-saving effect is better. For evaluating the energy-saving effect, you can refer to the proportion of no-load time to the total working time.
– Variable speed drive has more benefits:
- Reduce maintenance costs: Stable soft start reduces the impact on the power grid, extends the mechanical life of the motor and the whole unit.
- Make the air system more stable and reliable, reduce downtime and production losses. The energy-saving controller monitors more than 20 parameters, current, voltage, speed, torque, power consumption, and the system is highly intelligent.
- Reduces noise: when the amount of exhaust air decreases, the speed of the motor slows down, and the noise of the air compressor is much smaller than that at full speed. The time of unloading operation is reduced, and the noise of venting is also reduced.
Permanent Magnet Synchronous Motor
Permanent magnet synchronous motors are more efficient than The Asynchronous motors and have a wide high efficiency range:
– For the permanent magnet synchronous motor, when the speed range is 25% -99% of the rated speed, the efficiency can reach 95% -97%.
– But for the Asynchronous motor, only when the speed range is 70% -99% of the rated speed, the efficiency is about 88%. And what’s more, when the speed range is lower than 70% of the rated speed, the efficiency will drop sharply.
High Efficient components
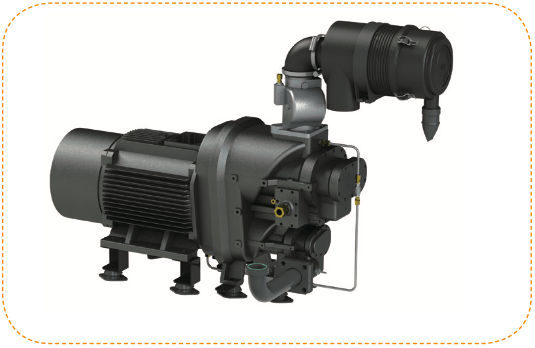
Patent Two-stage Dual-stage screw air end
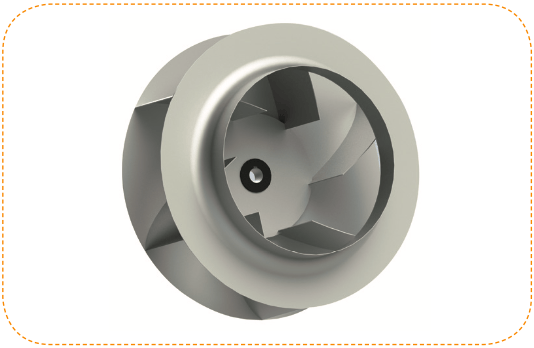
Dual cooling fan with Variable Speed Drive.
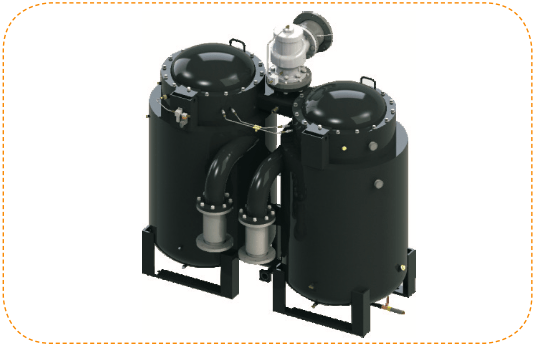
Redundancy design ensures lower oil content of compressed air and lower pressure loss.
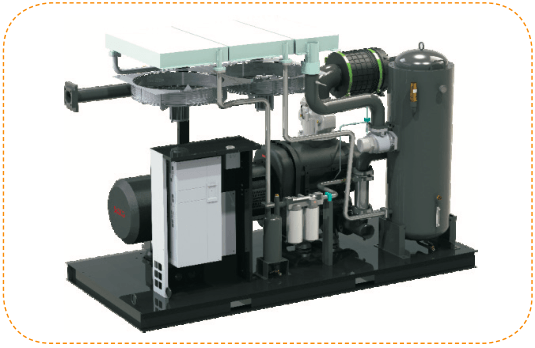
Every detail is optimized to the extreme, to ensure stability and reduce energy consumption loss.