Brewery Industry
Air Compressor for Brewery
Compressed air plays an essential role in the production of beer. Be it a large-scale production or a small craft producer – a reliable air compressor is important to give the users the perfect beer bottle. Although every brewery organization has different requirements for an air compressor such as the types of available compressors, size, focus, and other requirements of the brewery.
Regardless of the requirements, they are vital to ensure smooth and effective processes in the brewer industry.
Do you need
Class 0 Oil-free compressed air systems for your brewery production line?
|
|
Do you need
Low dew point and Clean compressed air for fewer rejections and better quality?
|
CONTACT US |
We have more than 30 years’ experience.
|
Use of an Air Compressor in a Brewery
Compressed air is used to ensure that yeast cultures get enough oxygen during the process of fermentation. Brewers also use compressors to ventilate water and transport solids like spent grains, whole malt, and sugar.
Compressed air is also used during bottling as it helps the beer to move from the conditioning tank to the individual bottles. It is also used to keep the lines clean and water-free. Compressed air is also used during the process of canning and clarifying the product. It controls valves and helps in the automation of the packaging and labeling process.
The process of the brewery is challenging but the use of an air compressor makes it easier. The existence of an air compressor is important in a brewery.
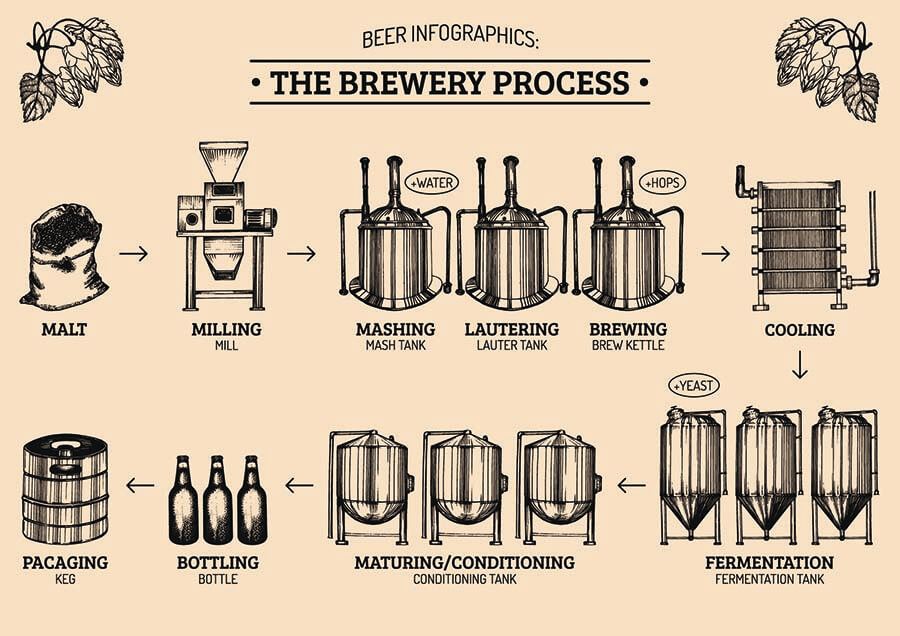
1 Moving Beer
The beer is often conditioned in a secondary tank. Compressed air is highly functional to make the transfer. The transfer of beer from conditioning tank to canning tank can be done with the help of compressed air although, ensure the line of transfer is dry and clean during the movement process.
2 Aeration
During the process of fermentation, oxygen is used for the fermenting yeast present in the beer wort in order to convert sugar into alcohol. Air compressors can help deliver oxygen in a controlled, efficient, and clean method.
3 Clarification
The process involves clarification of the haze from the beer. This gives the beer a cleaner taste and appearance. Air compressors are used in this process to remove the unwanted solid from the beer to make it worth drinking.
4 Equipment Cleaning
It is important to keep all pieces of machinery and lines clean through which beer passes. Air compressors help deeply clean the lines and ensure that they are free of contaminants. If the lines aren’t clean, the beer will not taste as intended and would result in being discarded. Cleaning machines and lines are important in order to keep the beer up to the mark.
5 Bottling
Air compressors are usually used for accurate bottling in the beer industry. It helps the bottle to get the right air pressure using the appropriate unit that plays a critical role. Pressurized air is vital for the process of moving beer to the bottles from the conditioning tank and to keeping lines clean and free of water. It is used to ensure bottling is done correctly so the beers can be stored for a longer period of time.
6 Glass bottle blowing
Compressed air goes into the form of bottles inside the forming machines, where all the parts that comprise the bottle — the lip, collar, neck, stem, shoulder, body, in–sweep heel, cavity and raised embossing — are formed. The forming stage consists of several steps, the pneumatic tools which can work on the outside shape of the bottle and another tool that is used to form the inside cavity.
Benefits of an Air Compressor in Brewery
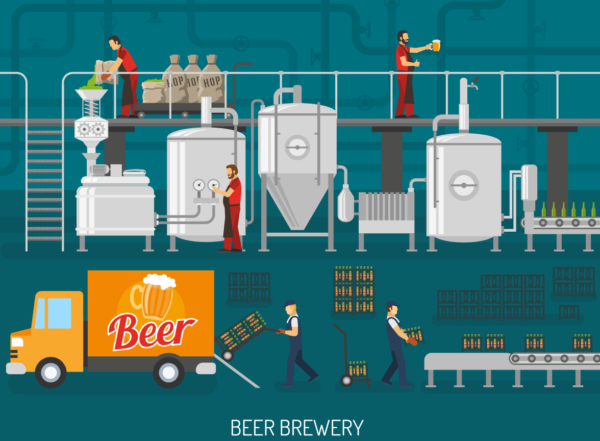
Implementing the use of air compressors in brewery have multiple benefits. A few of the basic advantages include:
- Versatility: air compressors provide a high-pressure needed for many operations in a brewery including bottling, capping, and cleaning.
- Continuous Use: the working hours of an air compressor are long. It will remain in operation throughout the brewing hours, for brewpub restaurants, and all operating hours.
- Consistent Flow: Not all compressors can work 24/7 but rotary compressors can. They are designed to deliver a flow of work for 24 hours straight although a piston air compressor would burn up.
- Efficiency: The use of an air compressor is efficient for the brewery. It helps maximizes productivity and is time-effective. It reduces the possibility of human error and can help you achieve your goals.
Types of Air Compressors Used in a Brewery
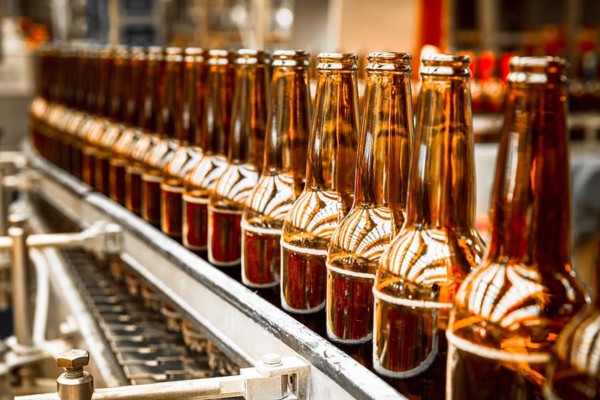
There are three types of air compressors that are used in the brewery.
1. Piston/ Reciprocator Air Compressor
Piston air compressors use a cylinder driven by a crankshaft in order to compress air. Piston air compressors are usually oil-lubricated but can be oil-free too is required. These air compressors feature either a single-stage or a double-stage feature. The single-stage piston brings air with a single stroke that goes about 120 PSI. On the other hand, a double-stage air compressor can go up to 175 PSI and can go additionally with a second attached piston.
Piston air compressors are usually used for low-pressure tasks, for instance, washing kegs.
2. Rotary Screw Compressor
These air compressors utilize a positive displacement system and a unique hydraulic seal used to transfer energy among the rotors. The design and rotation features allow the air to move through the compressor. Rotary Screw compressors are usually used for high-pressure tasks and bottling.
3. Scroll Compressor
A Scroll Compressor is comparatively less noisy as compared to a piston air compressor. It is oil-free and has comparatively low maintenance. Although, the noise-free scroll compressor gives a low pressure of 116 PSIG. It allows less CFM as compared to Piston Air Compressor of the same size.
Whilst choosing an air compressor for your brewery, you can choose between oil-lubricated and oil-free air compressors depending upon the need of your business.
It is known that brewing is one of the most rapidly growing industries in the brew market. The demand for the product is increasing by the day, and so is the production. Air compressors are highly beneficial for organizations in terms of productivity, efficiency, cleanliness, time-effectiveness, and a lot more. Air compressors vary as per the requirement of the brewer production. To know which air compressor is suitable for your brewer, talk to the experts at air compressor companies that will let you know what best suits your needs. To solve your problem TyPhoonCompressor has a wide range of air compressors with good build quality and a reasonable price.
Common Equipment for the Brewery Applications
- If the compressed air will be applied to brewery industry, we suggest using 100% Oil-free type air compressor with the refrigeration air dryer and filters.
- For a low-risk compressed air for production line, if with a limited budget, the oil-lubricated type air compressor with refrigeration air dryer and filters can be chosen, but for long term consideration, an oil-free type air compressor can not only produce high-quality oil-free and clean air but also costs lower for maintenance and energy.
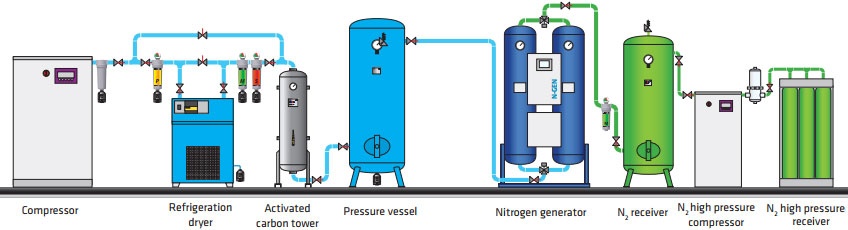