PET Blowing Industry
PET Air Compressor
High-pressure air compressor for PET Blowing
Not PISTON
No more high noise and vibration
|
|
SCREW TYPE
Patented Two-stage single-screw compression
|
|
Not BOOSTER
No more high maintenance costs
|
CONTACT US |
We have more than 30 years’ experience. |
As we know, PET(polyethylene terephthalate) is a safe and recyclable packaging material. Compared with aluminum cans and glass bottles, PET containers are more environmentally friendly and cost-effective.
Air compressors are the main utility for plastic processing plants, A large amount of compressed air is needed to blow PET or PP preforms into bottles.
|
|
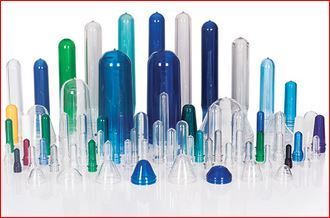 |
Typical Applications for PET Air Compressor
|
The Common Applications for PET Air Compressors?
|
PET Bottle blowing |
high pressure compressed air is used for blowing bottles.
The pressure depends on the container’s design, its wall thickness, blow speed and so on. The bottles with thick walls, sharp edges and special shapes need higher pressure. Generally, the stretch blow moulding requires about 10~25bar for pre-blowing and about 40bar for the bottle blowing process. The trend for PET bottle blowing machines is to reduce the blow pressure as much as possible for energy saving.
|
Cleaning |
The bottles should be cleaned by compressed air before filling the water, beverage, cooking oil and so on.
If the air is contaminated, it will influence the flavor and odor, causing health problems.
|
Filling |
Oil-free compressed air should be used in filling machines for liquid preparations. |
Packing and labeling |
Low pressure compressed air is also used for automated lines for packaging, labeling, and more. |
Instrumentation |
For pneumatic conveying during the manufacturing process.
For the control valves, sorting, polishing, and more.
|
Development for PET Air Compressor
There are compressor solutions for PET bottle blowing machines as follows:
Comparison |
Small Oil-lubricated Piston |
Oil-free Piston |
Booster |
Oil-free SCREW |
Photo |
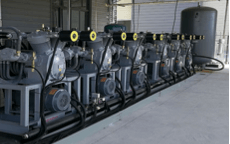 |
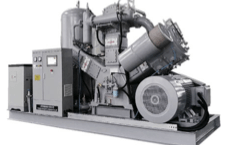 |
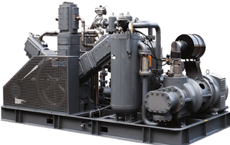 |
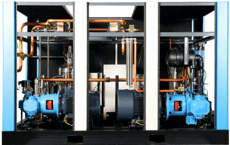 |
Lubricate method |
Oil-lubricated |
Oil-free (Class 1) |
Oil-free (Class 1) |
100% Oil-free (Class 0) |
Cooling method |
Air-cooled |
Water-cooled |
Water-cooled |
Air-cooled or Water-cooled |
Compression stages |
Two-stage/Three-stage piston |
Three-stage piston |
1st screw 2nd piston |
Two-stage SCREW |
Space for 40bar 6m3/min |
3800*1000*1700mm 2800kg |
3100*1750*2150mm 3400kg |
2790*1500*1470mm 3200kg |
2900*1400*1700mm 2100kg |
Comparison |
Piston type |
Screw type |
Working principle |
For piston compressors, the air is compressed in different cylinders and cooled. For example, the atmospheric air is compressed to 4~5bar in the first cylinder, then cooled before pushing to the second cylinder, achieving 15~17bar then, the air is cooled again and reaches 40bar finally. |
For screw type, the air is compressed to 7~8bar at the first screw compression stage, there is no need to cool and the air goes into the second stage screw air end, finally achieving 30~40bar air discharge directly without cooling. |
Efficiency |
Low-speed 600-1500r/min, more friction pairs, lower efficiency
High temperature:Energy lost due to hot air discharge
Shorter lifetime of the component |
Rotation speed 3000r/min, zero loads
About 50℃, no heat waste
Ideal isothermal compression |
Maintenance |
Complex structure needs special technical support for installation
High maintenance costs if routine checks are not done at 4000~6000 hours |
Simple and balanced structure
50000h lifetime, Less than $500/year |
Why Should We Choose Screw Type Compressor
30~40bar
Air Compressor:
Screw VS Piston
|
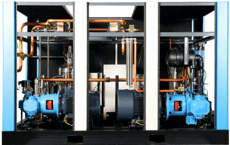 |
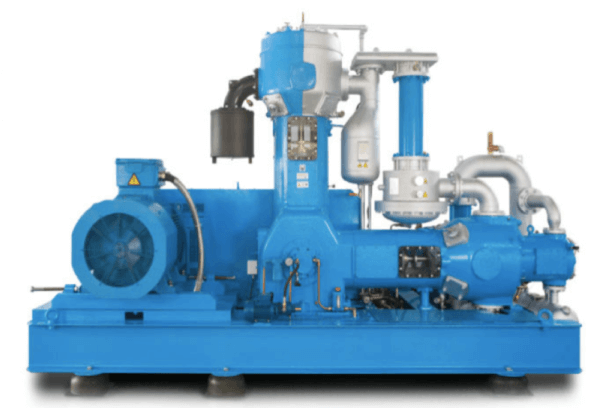 |
Comparison |
Oil free Screw Air Compressor |
Oil free Piston Air Compressor |
Air quality |
100% Oil-free |
Air cylinder Oil-free, Crankcase has oil |
Compression Method |
2 Stage Screw |
3 Stage Piston |
Lubricating Medium |
Pure Water |
None |
Temperature |
Low: < 55℃, No need for cooling |
High: 125~200℃, After cooling about 60℃ |
Cooling Method |
Air Cooled or Water Cooled (Only one cooler for lubricating water) |
Water Cooled (Two interstage cooler and one aftercooler for compressed air) |
Rotate Speed |
3000 r/min Ideal Speed |
600~900 r/min Low Speed |
Vibration and Noise |
Balance and Simple structure, low vibration, and less noise |
The pistons rise and fall or move back and forth causing too much vibration and Noise |
|
|
|
Costs – Purchasing |
More |
Less |
Costs – Foundation |
No costs |
Require foundation and grouting due to high unbalanced forces & high vibration. |
Costs – Maintenance |
Only Air filter elements and Water filter elements |
High wear & tear of moving parts like piston rings, valves, etc. |
Costs – Energy (e.g. 40bar 10m3/min) |
Motor Power: 112kW (1st stage 75kW+2nd stage 37kW) |
Motor Power: 132kW |
Capacity Loss |
There is no loss / very minor loss in Capacity over a period. |
There is De-ration in Capacity due to wear and tear in cylinder crank case, piston rings, pistons and valves. |
Quality Requirements for PET Air Compressor
Generally, the compressed air should be purified of contaminants before use. General contaminants are solid particulates, water vapor, and moisture, oil vapors. Which are in the atmospheric air, the lubricating oil for oil-injected type air compressors, the pipes, storage air tank, and distribution.
When the PET compressed air has a direct connection with drinking water or beverage, cooking oil, we must ensure purity and cleanliness to prevent contamination. For the details what we should do are as follows:
Remove the moisture
As we know, moisture is good for microorganisms and fungus growth. If there is moisture inside the pipes of the compressed air, it is easy to be blown to the products or the packaging or containers. So we need to use dryers to ensure the required dew point. Generally, for the direct contact compressed air, the dew point should be -40℃ and use a desiccant air dryer, and for low-risk non-contact compressed air, the dew point can be 3℃ and use a refrigeration air dryer.
Remove the oil
The oil exists in the atmospheric air, so even you choose a 100% oil-free type air compressor, there is still oil vapor in the compressed air, so the filters should be used.
Generally, for direct contact compressed air, use an oil-free type air compressor is a must. Ensures Class 0 100% oil-free compressed air with high purity, eliminates the health risk of rejection risk associated with oil contamination. For low-risk non-contact compressed air, we can use an oil-lubricated type air compressor which is more economical, but it’s better to use filters to ensure the oil content 0.003ppm.
Remove the particles
The atmospheric air includes solid particulates or dust that may cause contamination if contact with the products. Other contaminants may come from internal mechanisms of the air compressor system. We also need to use filters to ensure the particle content is no more than 0.01μm.
Common Equipment for the Pharmaceutical/Medical Applications
- For the direct contact compressed air for production line, we suggest using 100% Oil-free type air compressor with the desiccant air dryer and filters, the materials should be used is food-grade stainless steel.
- For the non-contact low-risk compressed air for production line, if with a limited budget, the oil-lubricated type air compressor with refrigeration air dryer and filters can be chosen, but for long term consideration, an oil-free type air compressor can not only produce high-quality oil-free and clean air but also costs lower for maintenance and energy.
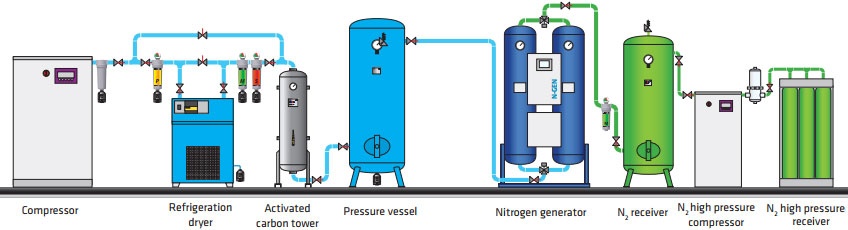