A rotary screw air compressor works on the principle of a positive displacement mechanism. In this mechanism, an air compressor draws in air through the inlet and increases the pressure over it. The increased pressure compresses the air and reduces its volume considerably.
To learn about the functioning of the rotary screw compressor, knowing about its various parts is necessary. Despite variation in sizes and construction, rotary screw compressors have some key parts that are common in all models. Let’s have a look at the key constituents of this air compressor.
Main Spare Parts of Rotary Screw Air Compressor
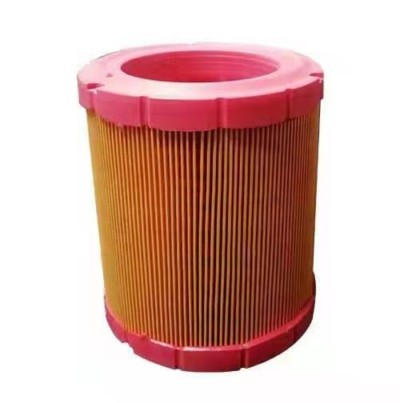
A rotary screw compressor consists of numerous layers of filters and an air filter is one of them. Dust and debris can clog the valves of the compressor and degrades its productivity. It eliminates debris, dust particles, and moisture from the air. By removing dust and moisture, it protects the compressor from damage.
Air filters are installed at the place where the compressor enters as well as in the piping that transfers compressed air from the compressor to the consumption area. The air filters at the entrance of air, air filters eliminate dust and dirt particles, so they do not damage the interior system. In the piping between the compressor and consumption, these filters purify the compressed air.
Air filters need are regular maintenance for effective performance. Cleaning them once in a while and replacing them regularly boosts the productivity of the compressor and it can work efficiently.
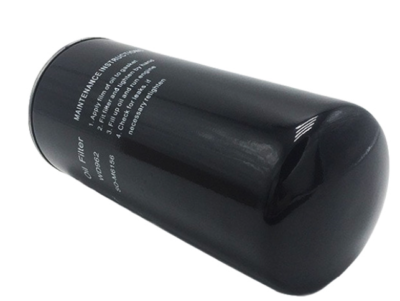
These filters are present in the walls of the rotating chamber as well as close to discharge valves. They eliminate oil from the air and purify the air. However, oil is required for cooling the compressor. The bypass valve in the oil filter allows some quantity of oil to flow that opens when the temperature of the compressor rises above a certain limit.

This component is a part of the oil-injected compressors. It is employed for the precise separation of oil and air mixture. It separates the oil from environmental air and provides a clear flow of compressed air.
Key Parts of Rotary Screw Air Compressor
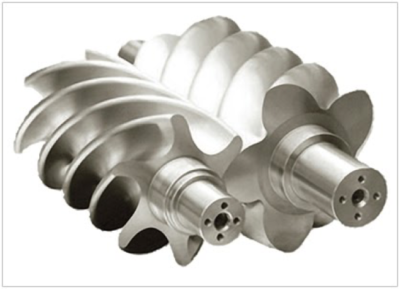
Rollers are the basic component of rotary screw air compressors and also known as rotors. Without them, a rotary screw compressor can do nothing.
Rotors comprise meshing helical screws and work in pair form. One rotor is referred to as the female rotor and the other one is called the male rotor. The female rotor usually comes with more flutes than the male rotor. The motor of the compressor rotates the male rotor and the female rotor is rotated by the male rotor.
The lobes of the male rotor function as a continuous piston that rolls down the flutes of the female rotor and drive the air in via a sealed series. It pressurizes the air and converts the regular air into compressed air.
The air is forced into the compressor by the rotors and leaves at the end of screws. The basic working unit that compresses the air is the volume between the male and female rotors. This volume of the inter-lobe area is large at the end where the air is taken in and it reduces remarkably along the length of the rotors up till the exhaust port.
At the entry of air, the male lobe is smaller than the female lobe. But as we move along the length of both rotors, the male rotor enlarges and the female one becomes smaller. At the outlet port, the space between the lobes of two rotors becomes extremely small. The reduction in the inter-lobe space compresses the ambient air and converts it into pressurized air at the end of the exhaust port.
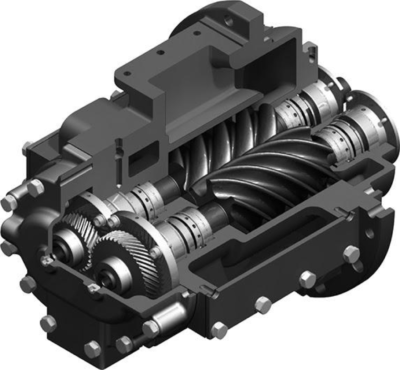
Compression cylinders offer an air-tight space that prevents the chances of leakage and facilitates the compression process. They are usually manufactured of steel and cast iron. It provides a secure place for the rotors to move alongside each other and provide a fine stream of pressurized air.
Compressor cylinders comprise numerous cooling techniques. In oil-injected screw compressors, cylinders also contain oil-lubricating units and distributing systems or maintaining a particular internal temperature.
Multiple cylinders or staged units with huge storage capacity are offered by industrial-grade rotary screw compressors. A wide variety of compressor cylinders is also available. You can find compressors with a single-cylinder powered by a single motor. Rotary screw compressors with multiple cylinders driven by multiple motors are also available.
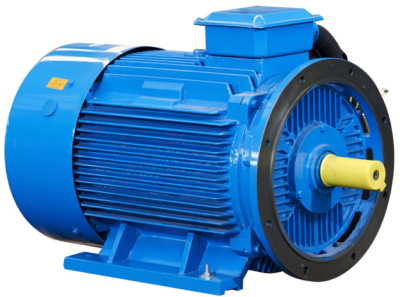
Like in other rotating gadgets, the rotary screw air compressor also has a rotating unit. This rotating unit is known as the motor. The motor provides energy to the rotors for rotation and thus runs the entire machine. Direct coupling is used for connecting motors to the compressors. Motors can also be attached to the compressors via pulleys and belts.
Usually, electromotors are employed for powering small, stationary compressors. For running medium and large rotary screw compressors, electromotors can’t generate enough power. To operate medium compressors, diesel engines are used. For powering large compressors, steam turbines are used that generate an enormous amount of energy. Using steam turbines instead of electromotors or diesel engines is a better choice as it is economical and safe to use.
Getting rid of excessive heat is necessary for the compressors as heat can lead them to un-repairable damage. Like all other types, the rotary screw compressor also has a cooling unit to lower the internal temperature. Compressor coolers assist in eliminating heat and maintaining a tolerable temperature within a compressor.
Cooler in small rotary screw air compressors comprises fins around the discharge pipes that are present between the compressor and the storage tanks. Large rotary compressors come with two coolers. One is the oil cooler, while the other is the aftercooler. An oil cooler is meant for lowering the temperature of the oil before it goes back to the compressor element. The aftercooler is designed to cool the high-pressure compressed air before it leaves the compressor.
It is a monitoring unit of the compressor. This component monitors and displays how well the components of the machine are working. It is the fastest and most accessible way to keep a check on the performance of the system. Regular monitoring of different parts of the compressor ensures the accurate functioning and productivity of the rotary screw compressor.
Some rotary screw compressors come with internal sensors that turn off the motor when no more compressed air is required as the storage tank is full. Some sensors also power off the motor after the completion of one cycle.
Other Parts of Rotary Screw Air Compressor
An Inlet valve is a tiny flap that resides on the top of the compressing unit and takes in the air from the environment. The flap sucks air into the compressor and thus is also referred to as a suction valve.
Inlet valves are available in various configurations. Variation in the designs assists in improving airflow. Three types of inlet valves are commonly used in rotary screw compressors. These are the poppet valve, ring valve, and plate valve. These valves comprise concentric layers that maximize the flow of ambient air from the environment into the compressor.
These valves are also known as discharge valves. They are present opposite to the inlet valve and release the compressed air without any leakage. By preventing leakage it helps to maintain the temperature and volume of the compressed air.
Outlet valves act as regulatory agents and carefully release compressed air into a storage container. These valves are sometimes attached to air houses for instant use. Maintenance and timely replacement of these valves are essential. Damaged outlet valves can not only ruin your air compressor but also jeopardize the humans and other equipment in the vicinity of the compressor.
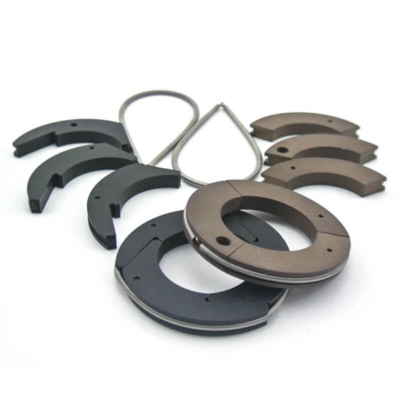
It is a circular seal that resides on the inlet valve and prevents the leakage of incoming ambient air. By preventing the leakage of ambient air, it boosts the efficiency of the compressor.
These bearings are present on the inlet valve and allow it to efficiently suck ambient air from the environment. Inlet bearings also ensure the continuous flow of air at a specific speed during the functioning of the air compressor.
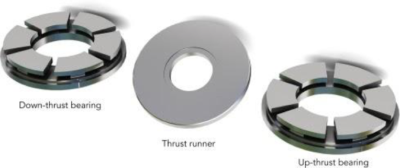
A rotary screw air compressor is perfectly engineered to make each part sturdy enough to function properly. Thrust bearings strengthen the interior construction of the compressor and make it work consistently. These bearings not only minimize the friction between various parts of the compressor but also stabilize the parts during movement.
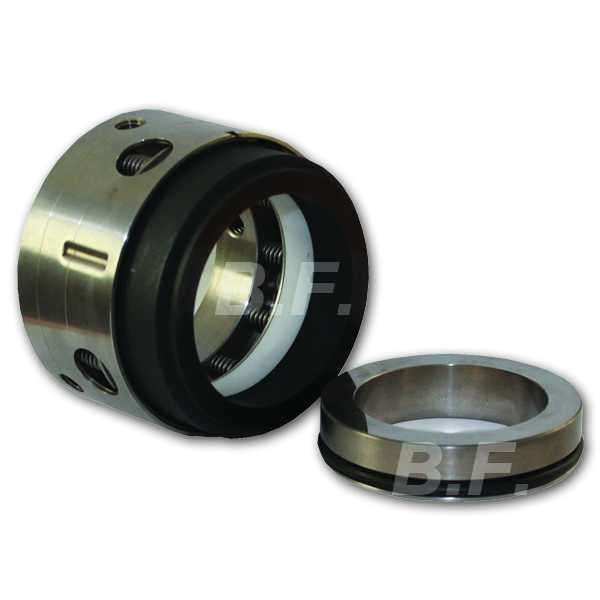
It is specially designed to prevent the leakage of the pressurized air outside. It keeps the compressed air in the compressor for a specific duration in case of any leakage. So, the rotary screw compressor can operate smoothly and produce high-pressure air.
Both these components are essential for making the air compressor leak-free. Gaskets and seals lock the interior and exterior components of the rotary screw compressor and seal them. They make the compressor airtight for smooth airflow and maintain the pressure of the compressed air.
Different parts of the rotary screw air compressor contain various gaskets and seals. Crankcase gasket, intercooler gasket, valve plate to head gasket, shaft seal, and oil seal are the most commonly used gaskets and seals used by the compressors. These tiny components of the air compressor not only enclose the pressurized air but also keep the contaminants away.
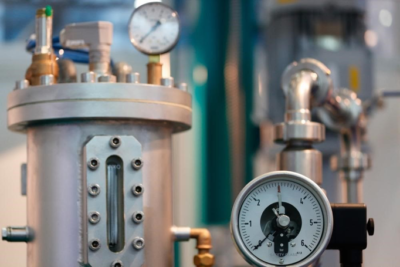
Gauges are used for monitoring the air pressure in the storage tank. Gauges are a necessary tool to keep a close eye on the air pressure. Daily checking pressure of air in the tank can help in detecting any change in the pressure immediately before it leads to any damage.
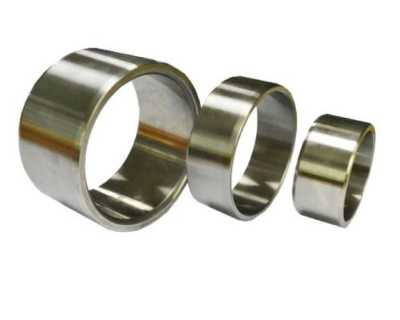
Bushings are meant to reduce friction by increasing the spacing between the parts of the air compressor that are in direct contact. By minimizing friction, protects the compressor from abrasive damage and reduces the risks of breaking down internal machinery.
This component of the rotary screw air compressor converts the mechanical energy of the compressed air into power. If the air movement is not perfect, the actuator will not generate enough air force. Like other components of a compressor, dust particles and debris also clog them and degrade their working capacity.