Printing Industry
Air Compressor for Printing Industry
A high-quality air compressing system is necessary for the printing department for so many reasons. Identifying the best compressor will improve your service’s efficiency and profits through quality products. After being in the printing industry for a few years, it’s pretty easy to take the importance of compressed air for granted. Printing processes can’t function properly without compressed air, be it high or low pressure. When it comes to printing equipment, there are multiples types of air compressors with their uniqueness.
Do you need
Class 0 Oil-free compressed air systems for your printing industry?
|
|
Do you need
Low dew point and Clean compressed air for fewer rejections and better quality?
|
CONTACT US |
We have more than 30 years’ experience.
|
Application of Air Compressor In Printing
Regardless of industrial screen printing or paper printing, air compressors likely have a vital task in your operations. They can energize a wide array of printing equipment in your facility. These printing tools can range from dryers to cylinders in a printing process. Apart from that, they can even help you out with various packaging duties.
To fully understand how they work, let’s look at the application of air compressors in printing equipment.
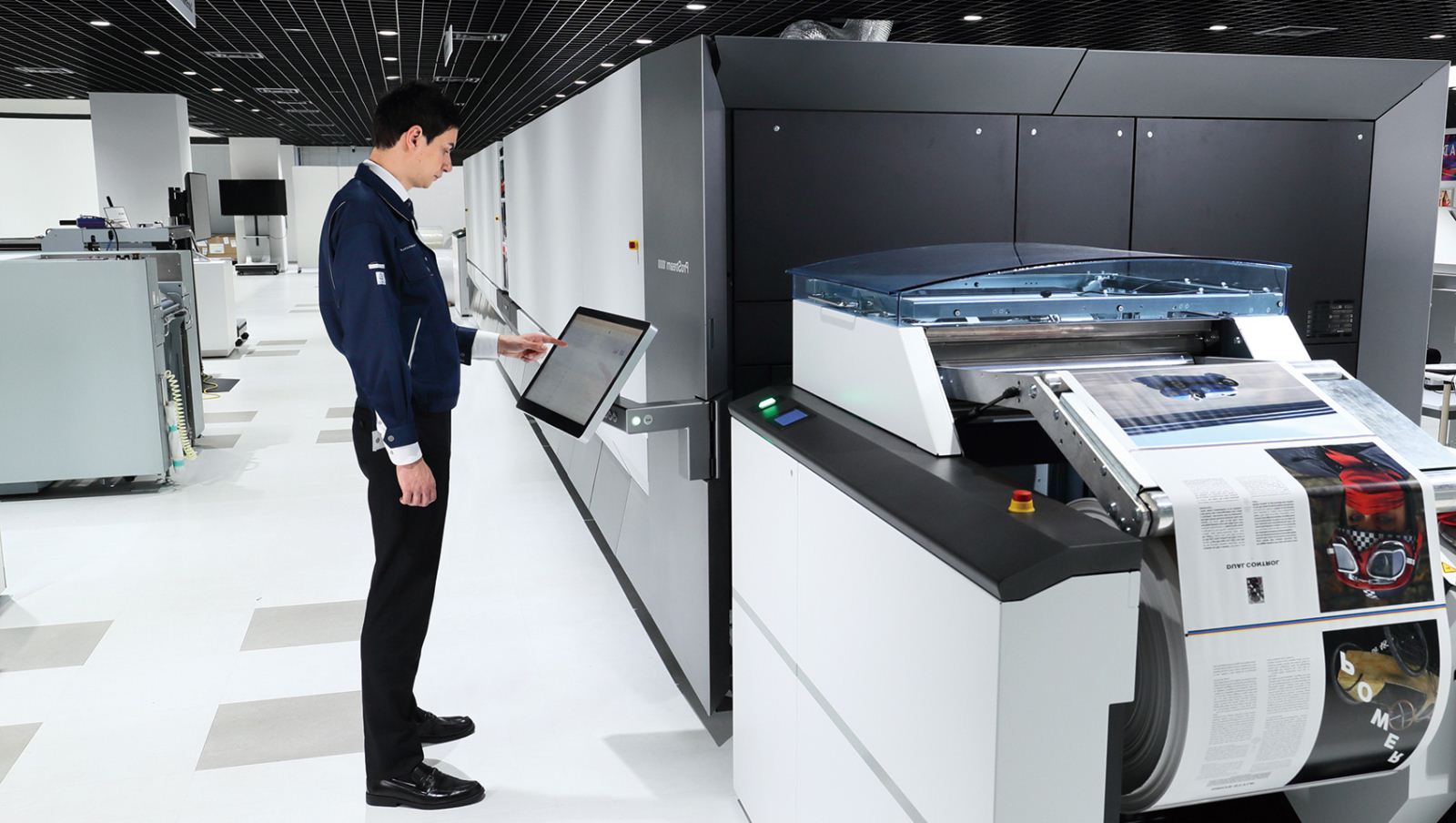
- Screen Printing
- Most screen printing machines require air compressors. These automatic screen printing machines heavily rely on the compressor, mainly because it powers many different components like the flash dryer and pressing unit. Any powerful air compressor will ensure that these parts keep moving smoothly and reliably and there’s no impairment in the printing process.
2 Paper printing
- The compressors also power printing tools such as collators, paper drills, folders, presses, cutters, vacuum pumps, and rollers. Cleaning the machine, lifting the type plate, pumping water, and operating the steam workbench and automatic type casting machine require compressed air. It helps with the brake mechanism, printing machine, folding machine, and other tension systems in the rotary concave printing space. Apart from that, it promotes pre-programmed merging to finish the printed material. Wrapping and binding are made simpler with inflatable clamps. The after-treatment equipment such as the air dryer, air filters help remove moisture and dust. This role is necessary when you’re operating with systems that need to preserve their cleanliness and dryness.
Benefits of using an air compressor in printing
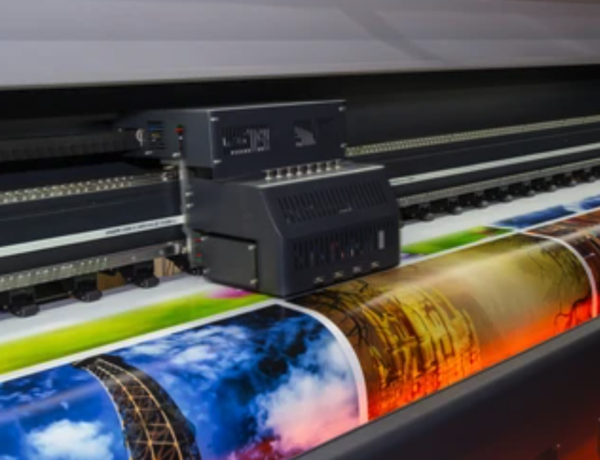
Many printing facilities use compressed air for a variety of purposes. One reasoning is that it allows for pneumatic automation. The additions that went into applying compressed air to automate the printing method are astounding. Pneumatic automation has two clear advantages:
- Increased efficiency
- Labor savings
When automation is present, one printing operator can perform multiple tasks. These programmed practices can also increase the effectiveness of a process and enhance production. Automation is often helpful to complete tasks. A pneumatic turntable in the bindery, for example, is quite repetitive. The use of a commercial printer simplifies the stacking process. The workers that used to do these mundane tasks manually can now perform more highly skilled functions.
Choosing the best equipment for your air compressor
Irrespective of the printing operation, other components have to back up your air compressor. These parts could range from a tank that holds compressed air to a dryer that removes excess and unwanted moisture. In extension to the additional elements, you should consider some factors for your air compression environment. Before getting the compressor that you want, make sure to check its loudness, space occupation, and power demands. Since an efficient system is essential, the last factor is especially crucial.
What are the types of air compressors used in printing?
Any dependable supply of compressed air is crucial to top-notch printing along with a pneumatic press. Since there are so many factors to consider, looking at every single air compressor can be perplexing. But there’s no need to worry because we’ll make it simple for you to understand. The various kinds of air compressors used in printing facilities are listed below.
- Reciprocating air compressor: These compressors work on an advanced reciprocation system, indicating forwards and backward movement. As they increase pressure in air to compress it, they are also known as piston compressors. When you look at the cylinder head, you will see the cylinder’s closed end. This closed-end of the cylinder connects to a free piston. A reciprocating air compressor typically works on energy from a diesel-powered engine. As far as these compressors are concerned, lubrication serves as the cooling mechanism for the operation. This lubricant undergoes a cooling process in the engine oil cooler and then recycles through the whole compressor.
- Oil-injected rotary screw air compressor: This compressor can be a good option for the pneumatic needs of a screen printing service. Rotary oil-lubricated screw compressors are more modern as compared to reciprocating air compressors. We know that they are more expensive than the traditional air compressor, but they also have a broad scope of advantages. In these rotary screw compressors, the lubricant serves four principal purposes. When oil enters the compression chamber through the injection, it cools the machine. Simultaneously, it also provides sufficient lubrication to all the moving components, provides adequate sealing, and helps with noise dissipation. Furthermore, the thermostatic device keeps a near-constant temperature by regulating the oil volume flowing to the lubricant cooler.
- Oil-free rotary screw air compressor: This type of air compressor ensures that there isn’t any oil in the compression chambers. In this configuration, the two separate rotors always stay apart from each other. Moreover, their positions are constant due to the lubricated timing gears located outside the compression cavities. This mechanism ensures that the air compressor’s output is entirely oil-free. When it comes to water-injected oil-free screw air compressors, water can perform the oil’s duties, such as cooling and lubrication. There are four types of oil-free rotary screw air compressors, including 2~5 bar Oil-free Screw Air compressors, 30~40 bar Oil-free Screw Air compressors, 7~10 bar Oil-free Screw Air compressors, and Super Energy Saving Series (8~40bar).
Many advantages make compressed air use in modern printing machinery mature and perfectly integrated, resulting in printing machinery that is more simplified, easier to operate and manage, and increasingly automated. With the increasing use of compressed air in printing equipment, the printing industry’s air compressor implementation has a bright future.
Common Equipment for the Printing Applications
- If the compressed air will be applied to printing industry, we suggest using 100% Oil-free type air compressor with the refrigeration air dryer and filters.
- For a low-risk compressed air for production line, if with a limited budget, the oil-lubricated type air compressor with refrigeration air dryer and filters can be chosen, but for long term consideration, an oil-free type air compressor can not only produce high-quality oil-free and clean air but also costs lower for maintenance and energy.
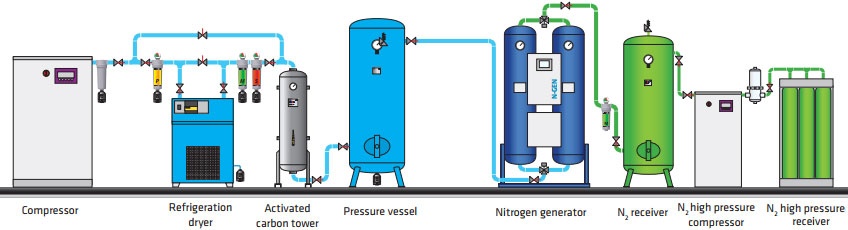