Wastewater Treatment
Air Compressor for Wastewater Treatment
High-pressure air compressor for Aerospace
Not PISTON
No more high noise and vibration
|
|
SCREW TYPE
Patented Two-stage single-screw compression
|
|
Not BOOSTER
No more high maintenance costs
|
CONTACT US |
We have more than 30 years’ experience. |
Applications for Water Treatment Air Compressor
Air compressors in wastewater management help treat wastewater for safe disposal or for further use in domestic or industrial contexts.
Wastewater treatment plants extract, separate, and process as much of the suspended solids in wastewater as possible.
The following are examples of applications of air compressors in the wastewater treatment process.
Slurry Liquid Pumps
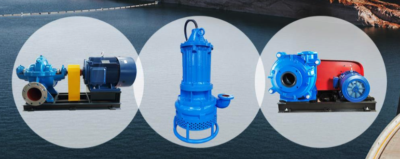
The slurry is a semi-liquid mixture of contaminants that floats in water and wastewater plants can have bio-solids, abrasive materials, and mud in the wastewater.
Slurry liquid pumps use air compressors to treat the water and process the slurry sourced from either industrial or domestic waste.
The air compressors ensure that the slurry is suspended while the wastewater is processed and the mixture separated and disposed of.
Air compressors provide enough pressure to transport the slurry between water tanks as the wastewater is treated.
Desalination
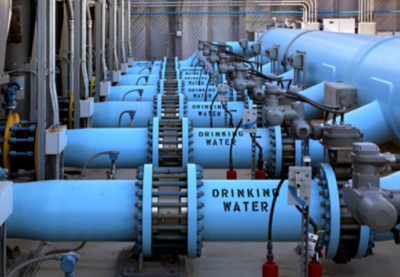
Backwashing is the process of pumping water in a backward motion through filters to get impurities or unwanted material, like sand, out of the water.
In wastewater treatment plants, air compression is intermittently used to backwash the water and break up the compact material by expanding filtration beds.
Air compressors pump purified backwash water and suspend sand particles that are later transported through sand filters and transported to disposal sites.
Backwashing Sand Filters
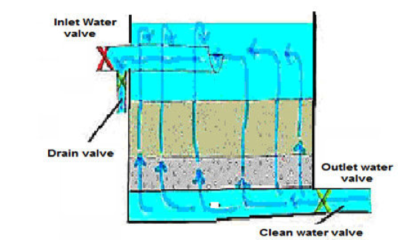
Backwashing is the process of pumping water in a backward motion through filters to get impurities or unwanted material, like sand, out of the water.
In wastewater treatment plants, air compression is intermittently used to backwash the water and break up the compact material by expanding filtration beds.
Air compressors pump purified backwash water and suspend sand particles that are later transported through sand filters and transported to disposal sites.
Purification
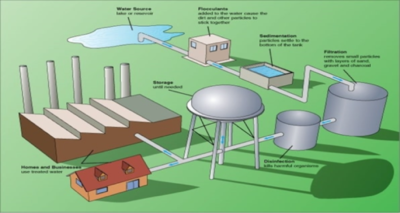
Wastewater is purified through air compressors to create viable, clean water for the safe run-off and disposal into rivers or seas or for the re-use of water in industries and domestic households.
If the wastewater is not purified, it could cause pollution and contamination of natural aquifers and household water supplies so purification is a crucial step.
Most wastewater plants use activated sludge tanks and air compressors to purify water to its maximum limit.
Activated sludge tanks first treat the water and then air compressors provide pressure to create heightened levels of oxygen for the water’s purification.
Removal and Disposal
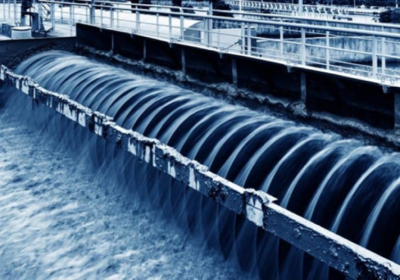
Air compressors are used in both the removal and disposal of wastewater and are vital for suction pressure in wastewater removal because they can remove impurities and flush out the undesired debris.
Air compressors provide an accurate level of suction pressure for sewer cleaning and can clean entire networks of sewerage systems where wastewater is transported.
Air compression in wastewater disposal is used for central vacuum systems in treatment plants that provide enough force to transport the wastewater towards disposal sites.
Digestion Tanks
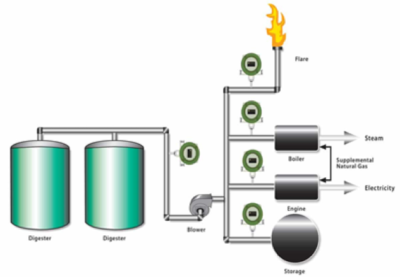
Digestion tanks in wastewater treatment employ anaerobic digestion to break down the solid, organic waste in sewage.
Air compression is used in the functioning, cleaning, and maintenance of digestion tanks.
A digestion tank causes sewage to decompose as the wastewater is run through clarifiers and wastewater digester gases are produced.
Air compressors play a vital role in digestion tanks as compressed air activates the tanks before oxygen is mixed with decomposing sewage so that gases can be created and retained.
Digester gases are a source of methane and serve as energy sources in other manufacturing processes.
Why Should We Choose Screw Type Compressor
30~40bar
Air Compressor:
Screw VS Piston
|
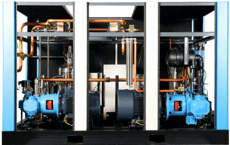 |
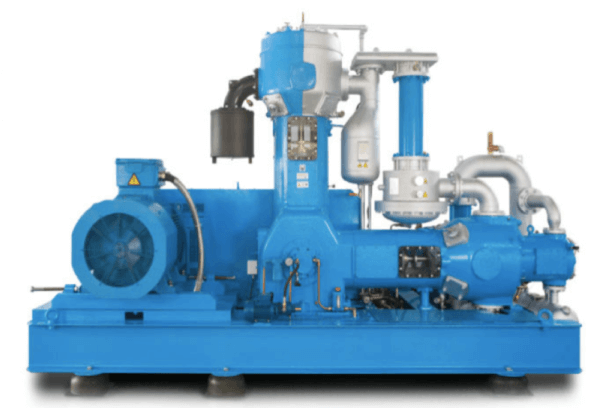 |
Comparison |
Oil free Screw Air Compressor |
Oil free Piston Air Compressor |
Air quality |
100% Oil-free |
Air cylinder Oil-free, Crankcase has oil |
Compression Method |
2 Stage Screw |
3 Stage Piston |
Lubricating Medium |
Pure Water |
None |
Temperature |
Low: < 55℃, No need for cooling |
High: 125~200℃, After cooling about 60℃ |
Cooling Method |
Air Cooled or Water Cooled (Only one cooler for lubricating water) |
Water Cooled (Two interstage cooler and one aftercooler for compressed air) |
Rotate Speed |
3000 r/min Ideal Speed |
600~900 r/min Low Speed |
Vibration and Noise |
Balance and Simple structure, low vibration, and less noise |
The pistons rise and fall or move back and forth causing too much vibration and Noise |
|
|
|
Costs – Purchasing |
More |
Less |
Costs – Foundation |
No costs |
Require foundation and grouting due to high unbalanced forces & high vibration. |
Costs – Maintenance |
Only Air filter elements and Water filter elements |
High wear & tear of moving parts like piston rings, valves, etc. |
Costs – Energy (e.g. 40bar 10m3/min) |
Motor Power: 112kW (1st stage 75kW+2nd stage 37kW) |
Motor Power: 132kW |
Capacity Loss |
There is no loss / very minor loss in Capacity over a period. |
There is De-ration in Capacity due to wear and tear in cylinder crank case, piston rings, pistons and valves. |
Common Equipment for the Water Treatment Applications
- If with a limited budget, the oil-lubricated type air compressor with refrigeration air dryer and filters can be chosen, but for long term consideration, an oil-free type air compressor can not only produce high-quality oil-free and clean air but also costs lower for maintenance and energy.
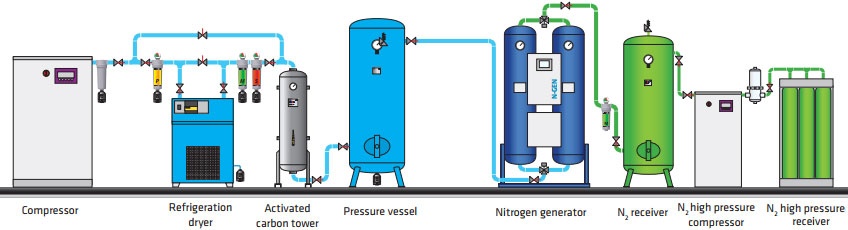