About TyphoonCompressor Desiccant Air Dryer
In compressed air systems, moisture is a huge problem and the prevention of corrosion caused by condensed water is an important issue. This is a critical factor as moisture and corrosion would minimize the performance and shorten the lifetime of compressed air systems and pneumatically controlled tools and equipment. To prevent this problem from occurring, the air dryer is the most commonly used solution. In these kinds of equipment, the main problems which affect the performance of compressed air systems are high volume, high pressure loss and complicated traditional types of heat exchangers which are not efficient. For this, TyphoonCompressor has successfully integrated the Brazed Heat Exchanger into our dryer system. This technology is supported by complete research and proven test data and the unique design has enabled TyphoonCompressor to obtain is being patented in France, USA, Taiwan and Southeast Asia.
Powerful Condenser
Our refrigerated air dryers offer a reliable, cost effective and simple solution to avoid condensation and corrosion in your systems.
Energy Saving
Fitted with Digital Scroll Compressors which adapt their refrigeration production according to of the thermal load to be dissipated, and allow great energy saving.
Easy to Maintain
On the rare occasion when servicing is needed, the enclosure design allows for direct access to all components allowing for easy maintenance of the dryer.
Desiccant Dryer Components
Electrical heater
Stainless steel material , simple structure.
High mechanical strength, high efficiency and long service life.
Air blower
High mechanical efficiency, low noise, stable and reliable operation.
PLC program controller
With LCD touch screen display working process and easy for user to check and setting the parameter.
The PLC program can auto switch the valve.
With alarm , Interlocking function, effectively monitor the operation process of the equipment, ensure reliable operation , convenient operation and maintenance.
Activated alumina
Good adsorption capacity, high strength, high water resistance, easy regeneration for system.
Pneumatic value
Pneumatic butterfly valve
Big rotational torque
Response quickly
Long service life
With nice seal performance, the seal parts use PTEE material.
With the feedback switch for the valve signal.
EXR Series Heated Desiccant Dryer
Description
Heated desiccant air dryer with heater on system compare to heatless dryer. The desiccant adsorb the moisture under the working preisute, use the heating compreseed air on generation process For that way, can save air loss than heatless type dryer.
System Flowchart
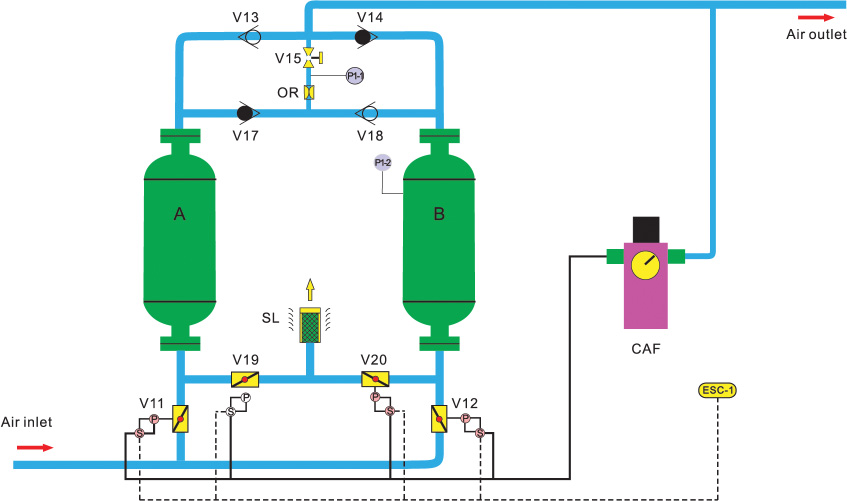
Main Parts
Heater element
Control system
Check valve
Activated alumina
Solenoid valve T
Pneumatic T valve
Pneumatic butterfly valve
Working Principle
Heated regenerating desiccant dryers are adopted with techniques of twin tower variable pressure absorbing and heating regeneration. During the regeneration progress, the depressurized expanded dry air is heated to a certain degree to enable it with more absorbing capability while reducing the use of regenerated air compressed air is dried through one tower while the other desiccant tower is being regenerated. The principle of the heated regenerating desiccant dryer is: One absorbing tower performs absorbing under working pressure while another one distills some of the compressed air from the main pipe then depressurizes and heats is for regenerated use. The heated regenerated desiccant contains less water and improves the absorbing capability.
Technical Specification
- Energy-saving with air loss lower than 6%
- High performance of the whole system by long switch cycle.
- Main parts use famous brands to ensure equipment continuous stability.
- Temperature protection is adopted to avoid damage from overheating.
- Adopted with low power consumption electrical components to improve the heating capability.
Optional Configuration
- Molecular sieve
- Dew point displaying, dew point as low as -70 ℃
- High dew point alarm/lock, Higher inlet temperature up to 50 ℃
- Mounted air filters
- PLC LCD monitor, communication port, and special voltages.
Technical Specifications: EXR
|
Flow Capacity
|
Air Conn. (BSP)
|
Dimensions
|
|
|
MODEL
|
m3/min
|
m3/h
|
CFM
|
Width
|
Length
|
Height
|
Weight (kg)
|
Heater (kw)
|
EXR-5
|
0.7
|
42
|
25
|
1/2”
|
500
|
690
|
915
|
180
|
0.9
|
EXR-10
|
1.6
|
96
|
56
|
1”
|
500
|
690
|
1298
|
190
|
0.9
|
EXR-20
|
2.6
|
156
|
92
|
1”
|
500
|
780
|
1324
|
280
|
1.5
|
EXR-30
|
3.8
|
228
|
134
|
1”
|
540
|
860
|
1350
|
320
|
1.5
|
EXR-60
|
7
|
420
|
247
|
1-1/2”
|
700
|
1010
|
1558
|
480
|
2.4
|
EXR-75
|
8.5
|
510
|
300
|
1-1/2”
|
700
|
1010
|
1785
|
540
|
2.4
|
EXR-100
|
11.5
|
690
|
406
|
2”
|
800
|
1240
|
2232
|
650
|
4.5
|
EXR-120
|
13.5
|
810
|
476
|
2”
|
800
|
1240
|
2232
|
690
|
4.5
|
EXR-150
|
17
|
1020
|
600
|
DN65
|
860
|
1280
|
2260
|
780
|
5.4
|
EXR-200
|
23
|
1380
|
812
|
DN65
|
860
|
1700
|
2477
|
920
|
7.5
|
EXR-250
|
27
|
1620
|
953
|
DN65
|
930
|
1320
|
2570
|
1050
|
9
|
EXR-300
|
34
|
2040
|
1200
|
DN80
|
960
|
1700
|
2626
|
1200
|
10.8
|
EXR-400
|
45
|
2700
|
1588
|
DN100
|
1060
|
1750
|
2646
|
1530
|
15
|
EXR-500
|
55
|
3300
|
1941
|
DN100
|
1060
|
1850
|
2646
|
1750
|
18
|
EXR-600
|
65
|
3900
|
2294
|
DN125
|
1240
|
2160
|
2784
|
2230
|
22.5
|
EXR-800
|
87
|
5220
|
3071
|
DN150
|
1440
|
2416
|
2827
|
2710
|
28
|
EXR-1000
|
110
|
6600
|
3883
|
DN150
|
2120
|
2980
|
2990
|
4130
|
37.5
|
EXR-1200
|
130
|
7800
|
4589
|
DN150
|
2220
|
3080
|
3030
|
4700
|
45
|
EXR-1500
|
160
|
9600
|
5648
|
DN200
|
2320
|
3180
|
3316
|
5800
|
56
|
EXR-2000
|
210
|
12600
|
7413
|
DN200
|
2520
|
3380
|
3360
|
7370
|
72
|
EXR-2500
|
260
|
15600
|
9178
|
DN250
|
2720
|
3580
|
3596
|
9020
|
90
|
EXR-3000
|
320
|
19200
|
12708
|
DN250
|
2970
|
3580
|
3606
|
11900
|
112.5
|
EXR-3500
|
360
|
21600
|
14473
|
DN300
|
3220
|
3720
|
3720
|
13100
|
124.8
|
EXR-4000
|
410
|
24600
|
14473
|
DN300
|
3370
|
3910
|
3910
|
14800
|
145.8
|
EXR-5000
|
510
|
30600
|
18003
|
DN300
|
3600
|
4200
|
4200
|
16000
|
170
|
Technical Specifications: KXD + CT
|
Flow Capacity
|
In/Out
|
Dimensions
|
|
Carbon Tank
|
Activated Alumina
|
MODEL
|
m3/min
|
m3/h
|
CFM
|
Connection
|
Width
|
Length
|
Height
|
Weight (kg)
|
Size
|
Weight (kg)
|
KXD-5
|
0.7
|
42
|
25
|
1/2”
|
500
|
1050
|
915
|
180
|
7.5L
|
14
|
KXD-10
|
1.6
|
46
|
56
|
1”
|
500
|
1050
|
1298
|
290
|
14L
|
32
|
KXD-20
|
2.6
|
156
|
92
|
1”
|
500
|
1190
|
1250
|
420
|
26.3L
|
52
|
KXD-30
|
3.8
|
228
|
134
|
1”
|
540
|
1320
|
1276
|
480
|
42L
|
76
|
KXD-50
|
6
|
360
|
212
|
1-1/2”
|
600
|
1470
|
1805
|
680
|
71L
|
120
|
KXD-60
|
7
|
420
|
247
|
1-1/2”
|
700
|
1645
|
1588
|
720
|
78L
|
140
|
KXD-75
|
8.5
|
510
|
300
|
1-1/2”
|
700
|
1645
|
1727
|
810
|
89L
|
170
|
KXD-100
|
11.5
|
690
|
406
|
2”
|
800
|
1900
|
1958
|
980
|
130L
|
230
|
KXD-120
|
13.5
|
810
|
476
|
2”
|
800
|
1900
|
2232
|
1040
|
160L
|
270
|
KXD-150
|
17
|
1020
|
600
|
DN65
|
860
|
1960
|
2360
|
1170
|
197L
|
340
|
KXD-200
|
23
|
1380
|
812
|
DN65
|
860
|
2000
|
2477
|
1380
|
266L
|
460
|
KXD-250
|
27
|
1620
|
953
|
DN65
|
930
|
2600
|
2570
|
1580
|
320L
|
540
|
KXD-300
|
34
|
2040
|
1200
|
DN80
|
960
|
2700
|
2626
|
1800
|
400L
|
680
|
KXD-400
|
45
|
2700
|
1588
|
DN100
|
1060
|
2830
|
2646
|
2300
|
540L
|
900
|
KXD-500
|
55
|
3300
|
1941
|
DN100
|
1120
|
2900
|
2730
|
1630
|
656L
|
1100
|
KXD-600
|
65
|
3900
|
2294
|
DN125
|
1240
|
3300
|
2784
|
3350
|
808L
|
1300
|
KXD-800
|
87
|
5220
|
3071
|
DN150
|
1500
|
3700
|
2827
|
4070
|
1100L
|
1740
|
KXD-1000
|
110
|
6600
|
3883
|
DN150
|
1700
|
4150
|
3038
|
6200
|
1400L
|
2200
|