Laser Cutting Machine
Air Compressor for Laser Cutting Machine
Laser Cutting Machines are in high demand around the globe. They can cut material in the most precise, quick, and efficient way. Thus, unlocking various domestic and industrial applications.
Initially, these laser cutting machines were expensive to use and maintain. Besides, they were not very efficient. This forced laser cutting machine manufacturers and engineers to develop innovative ideas to improve the result and reduce costs.
This is where the idea of using air assistance kicked in, which required air compressors to work.
Thus, the high usage and maintenance cost of laser cutting, the rising demand of its machines, and their reliance on compressed air enabled the air compressor manufacturers to customize their product to meet the demanding requirements, reduce cost and improve the cutting efficiency.
Although Air Assisted Laser Cutting machines are available in various types and sizes, they all need a pressurized gas source as power when working.
Do you need
12~16bar oil-lubricated screw air compressor for your laser cutting machine?
|
|
Do you need
20~40bar high pressure compressed air for your high precision fiber laser cutting machine?
|
CONTACT US |
We have more than 30 years’ experience.
|
Importance Of An Air Compressor for Laser Cutting Machine
To understand the importance of air compressors in laser cutting, it is essential to know how laser cutting works.
The process starts with a laser beam, which penetrates material with extreme heat by liquefying or melting it away, causing the residue to accumulate around the burnt section.
This is where air compressors are required. The compressed air or other pressurized gas sources (coaxial with the beam) is blasted on the target simultaneously, forming a jet that expels the residual material from the surface. This makes the cutting process fast, leaving behind smooth and flat, with no burry result.
The introduction of compressed air has enabled the laser cutting machine to cut a wide range of materials, from light fabric to harder metals and gemstones, with high precision, accuracy, and consistency.
An operating mechanism creates and stores the energy to operate a circuit breaker. Compressed air becomes the energy source for the Pneumatic operated mechanism for closing and tripping the hi-voltage circuit breakers. These pneumatic circuit breakers are called “Air Blast Circuit Breakers.”
The air compressor stores the compressed air in the storage tank (air receiver). When needed, it is blasted into the arc extinction chamber. This pushes away the moving contact. As a result, the connections are pulled apart, and the air blast moves the ionized gas away along with it and supports the arc extinction.
Types Of Pressurized Gas Sources Used In Air Assisted Laser Cutting Machines
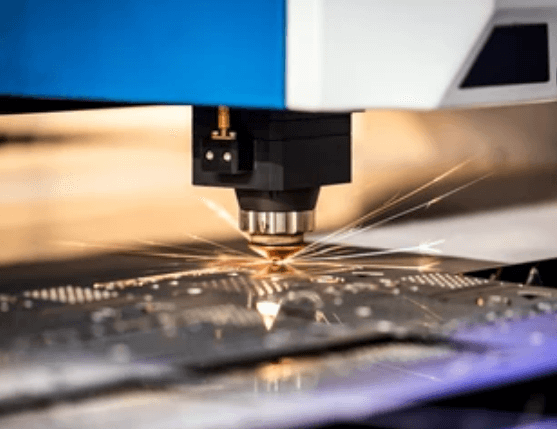
For the laser cutting process’s efficiency, not all types of gases are used as a pressurized gas source in laser cutting machines. Thus, there are only a few types of gases used for the process:
Oxygen
The use of pure oxygen as a pressurized gas source, blasted onto the material surface from the air compressor, performs three critical roles. First, the pressurized oxygen expels residual material away from the cut surface. Second, it acts as an oxidation agent to support the melting process of the metal. Last, it also improves the rigidity and hardness of the processed material.
Nitrogen
Nitrogen is a heavy gas that prevents the oxidation process, so it doesn’t enhance the heat transfer process or improve the laser cutter’s heating capability. However, it does form a protective layer around the molten metal hence preserving the surface’s quality. It gives high-quality cutting but increases air compressors’ power consumption, which leads to the high cost of cutting. Therefore, it is only used when processing requirements are pretty high or when processing the precious metal.
Air
Naturally, air comprises 21% oxygen and 78% Nitrogen. The other gases occupy the rest. Therefore, it can work as a pressurized gas source if dried to remove water vapors and filtered to remove unwanted gases or contamination. These unwanted gases can either inhibit the oxidation property, increase the air compressor’s power consumption, or hinder the molten material’s expulsion due to low density.
Besides the laser cutting machines, air compressors are also vital parts of nitrogen and oxygen generation systems. These individual generation systems can be used to produce purity gases (instead of buying cylinders), which are later to be used as a pressurized gas source in the laser cutting process.
Applications of Laser Cutting Machines with Air Compressors
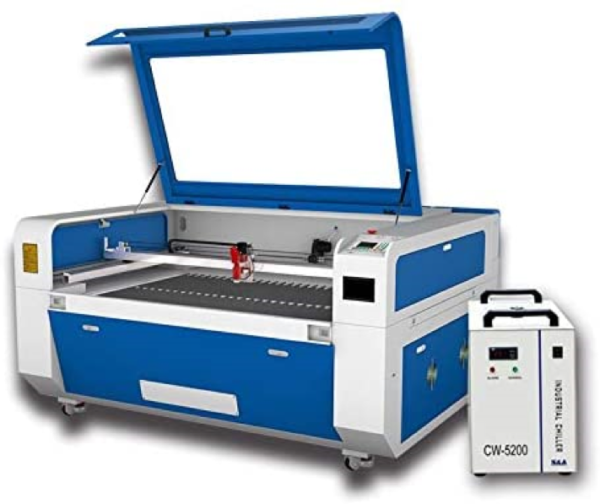
The introduction of air compressors in laser cutting machines has open doors to a plethora of industrial applications. Here are some of the common ones:
Metal Sheet Cutting
Cutting metal sheets into desired shapes was nearly impossible until laser cutting. The computerized laser cutting machines with air compressors can instantly turn metal sheets, including steel, aluminum, metal, tungsten, and nickel, into any ideal shape with clean cuts and smooth finishes. These shapes can be used in building structures, airplanes, and machine components.
Signage Cutting
Apart from Signage Cutting, air-assisted Laser cutting machines also engrave and cut plastic for other purposes. Although plastic cutting can be done from various other methods, through laser cutting, you can achieve high-quality results quickly
Plastic Cutting
Naturally, air comprises 21% oxygen and 78% Nitrogen. The other gases occupy the rest. Therefore, it can work as a pressurized gas source if dried to remove water vapors and filtered to remove unwanted gases or contamination. These unwanted gases can either inhibit the oxidation property, increase the air compressor’s power consumption, or hinder the molten material’s expulsion due to low density.
Glass Cutting and Engraving
Ever wondered how these modern vine glasses, glass mugs, and glass doors are crafted with beautiful, smooth, engraved, and detailed designs? It is all due to laser cutting machines with air compressors.
Advantages of Laser Cutting Machines with Air Compressors
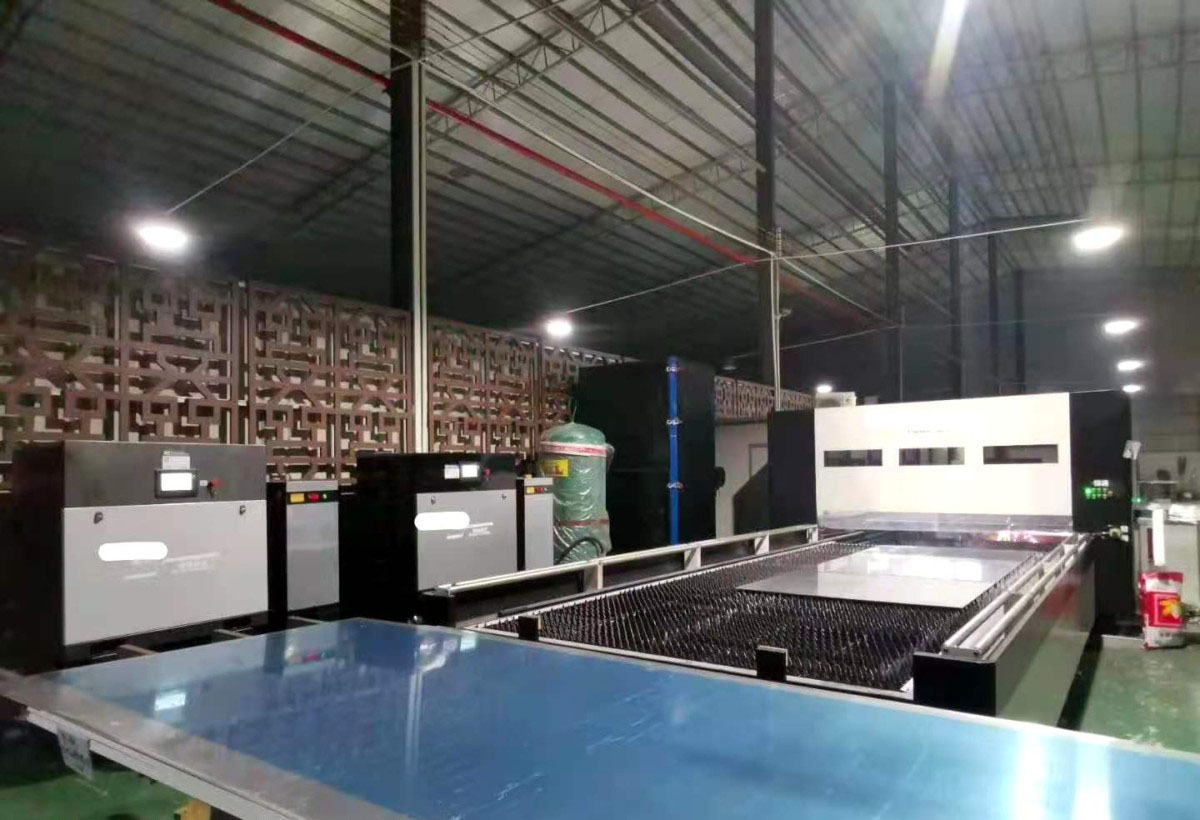
Air-Assist Laser Cutting Machines are massively popular due to the following benefits:
Time-Saving
Laser Cutting is an instant process, which is further accelerated with a compressed gas blowing mechanism. Thus, enabling the machine to cut any material in significantly less time.
Ability to cut various materials
Thanks to the introduction of air compressors in laser cutting, you can precisely and accurately cut an array of materials, from soft fabric to hardest precious stones and metals, into the desired shape.
Complex Designs
As laser beams can reach any place of the material at any depth, you can craft detailed and complex designs easily on various materials. And thanks to compressed air, the results are more precise, smooth, and economical.
Reduce Wastage
As the air compressor blows away the residue from the cutting material, the laser beam can only focus on their targets without wasting material, time, and energy.