Air Compressor for Gas Generator
Many industries have multiple needs for a constant supply of high-purity gases like oxygen and nitrogen.
These gases are transported in cylinders on site. However, it has several downsides like delivery cost, waiting time, limits supply, and risk of contamination.
Thus, industries are now switching to better, safe and cheap solutions like on-site Gas Generators.
One of the main components of gas generators is air compressor. Let dig down and learn how air compressor works in the gas generator industry.
Do you need
Class 0 Oil-free compressed air systems for your gas generator processing line?
|
|
Do you need
Dry and Clean compressed air for your oxygen/nitrogen generating line?
|
CONTACT US |
We have more than 30 years’ experience.
|
Air Compressor in a Gas Generator
Most on-site Gas Generators need air compressors to work. Among compressors, oil-free screw air compressors are the most reliable and energy-efficient. Moreover, they are also quiet and require low maintenance.
The oil-free screw air compressors can perform multiple functions, including:
- Increase the air pressure to the desired level, required by nitrogen or oxygen generation system to purify either through a Pressure Swing Adsorption (PSA) system or through a membrane.
- Increase the pressure of output gas to the desired level, usually in VPSA Oxygen Generators.
The oil-free screw air compressors are available in four types which you can use in gas generators according to pressure and airflow requirements.
The types are as follow:
Air Compressor in Nitrogen Gas Generators
Air Compressors are essential parts of Nitrogen Gas Generators, as these generators extract pure nitrogen from compressed air by separating nitrogen from oxygen and other gas molecules.
Pure nitrogen is helpful for many industrial applications, including removing oxygen and strengthening materials. It is also used in industries like food packaging, chemical plants, electronics, pollution control, mining, pharmaceuticals, oil and gas, military, and aerospace.
Two main types of nitrogen generators use air compressors:
PSA Nitrogen Generator
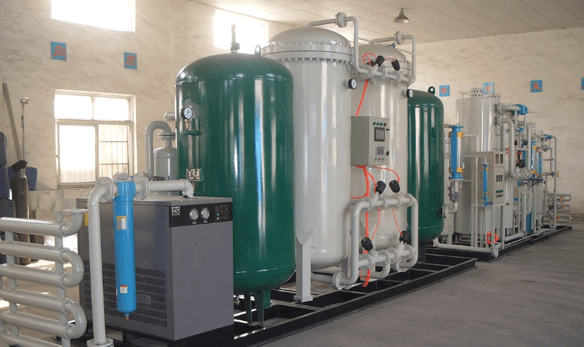
Also known as Pressure Swing Adsorption (PSA) Nitrogen Generators.
Its multi-stage purification process makes it better than the Membrane Nitrogen generator. It gives purified output, between 95% to 99.9995%, and consistent performance.
A Typical PSA Nitrogen Generator consists of an air compressor, inlet filters, pair of carbon molecular sieves (CMS), air dryers, buffer tanks, outlets, control valves, and sensors.
The air compressor pressurizes the air, and the air dryer dries it. Then the inlet filers remove impurities.
Next, the purified air enters the first pressurized sieve. The oxygen separates under high pressure, leaving behind pure dry nitrogen. The dry nitrogen is then stored in the nitrogen buffer tank.
After the first pressurized sieve is concentrated, it is depressurized and left for regeneration. Meanwhile, the purified air switches to the second pressurized sieve for the nitrogen extraction process.
Membrane Nitrogen Generator
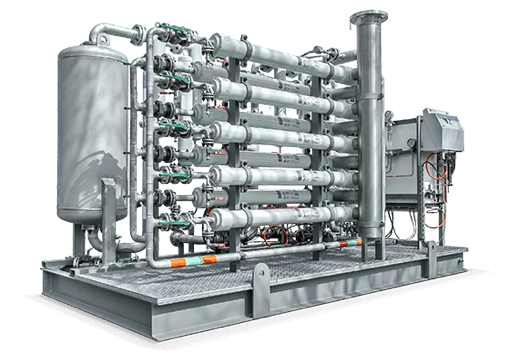
This generator consists of an air compressor, inlet filers, dryer unit, air heater (optional), membranes, and nitrogen storage reservoir.
The air enters the air compressor through an inlet. It is compressed to achieve the desired pressure and then delivered to inlet filters. These filters remove impurities from the air.
Next, the purified air passes through the hollow fiber membrane. The unwanted gases, including oxygen, diffuses out at different speeds depending on their molecular structure. This leaves behind heavier, slower-moving yet pure nitrogen gas molecules. The pure nitrogen is then collected to buffer tanks for use.
These gas generators are compact, quiet, and efficient. But they can only produce 95% to 99.9% pure nitrogen at a slower rate.
Air Compressor in Oxygen Generators
Oil-Free Screw Air compressors are also a vital component of Oxygen Gas Generators. Industries use these on-site oxygen generators to increase their productivity and efficiency. They are also safe and cost-effective.
Three main types of oxygen generators use air compressors:
Pressure Swing Adsorption (PSA) Oxygen Generators:
The PSA Oxygen Gas Generators work on the same principles as Pressure Swing Adsorption Nitrogen Generators. It uses absorbent materials like zeolites as a sieve to extract pure oxygen from compressed air. This technology can result in 90-99% oxygenated gas.
VPSA Oxygen Generator
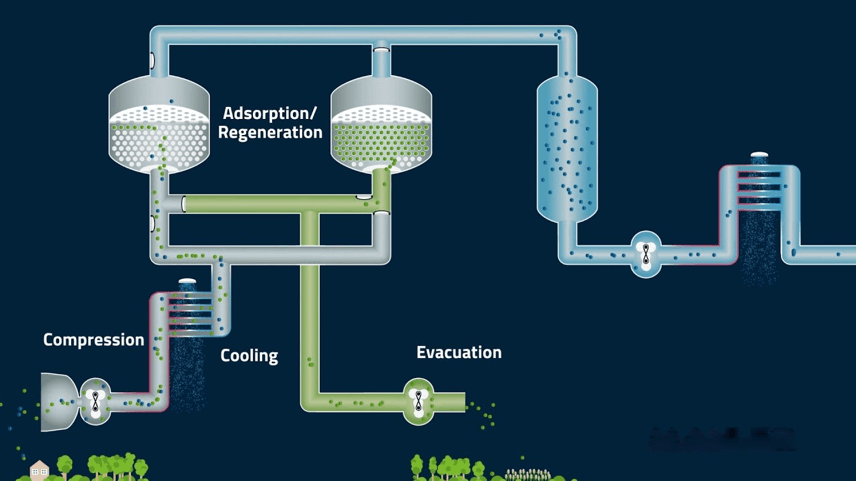
These oxygen generators use Vacuum Pressure Swing Absorption technology, where less pressurized air enters the system using a blower instead of air compressors. Moreover, a Vacuum pump sucks out waste gas and assists the sieve’s regeneration process.
You can also use a 7~10bar oil-free screw air compressor as an oxygen booster. It is to get higher oxygen pressure for output supply. This technology can result in 90-95% oxygenated gas.
The VPSA Oxygen Generator comprises air blowers, air filters, air coolers, silencers, two carbon molecular sieves (CMS), vacuum pump, oxygen buffer, and oxygen booster compressor.
The air goes through series of filers to remove impurities. Then air blowers and air coolers compress and condition the air.
The purified air is then fed into one of the absorption towers containing zeolites as a sieve. Here, the Zeolite surface absorbs the nitrogen in the air, leaving oxygen at desired purity.
Once the nitrogen level in the first tower concentrates, it is left for regeneration using a vacuum pump. While the purified air switches to another sieve for the same absorption process.
The purified oxygen is then compressed to the desired level by the air compressor and stored in a compressed oxygen buffer tank for output supply.
Membrane Oxygen Generator
They are considered one of the reliable oxygen generating systems due to no moving part that can fail.
This generator consists of an air compressor, inlet filers, dryer unit, membrane, and oxygen storage reservoir.
The air enters the air compressor through an inlet. It is compressed to achieve the desired pressure and then delivered to inlet filters.
These filters remove impurities from the air. Next, the purified air passes through the hollow fiber membrane, where oxygen diffuses out at certain speeds depending on its molecular structure, leaving behind other gases.
The oxygen is then filtered out from the remaining gases and collected in the oxygen buffer tank.
These gas generators are compact, quiet, and efficient. But they can only produce 95% to 99.9% pure oxygen at a slower rate.
Common Equipment for the Gas Generator Applications
- If the nitrogen or oxygen will be applied to food and medical industry, we suggest using 100% Oil-free type air compressor with the desiccant air dryer and filters, the materials should be used is food-grade stainless steel.
- For a low-risk compressed air for production line, if with a limited budget, the oil-lubricated type air compressor with refrigeration air dryer and filters can be chosen, but for long term consideration, an oil-free type air compressor can not only produce high-quality oil-free and clean air but also costs lower for maintenance and energy.
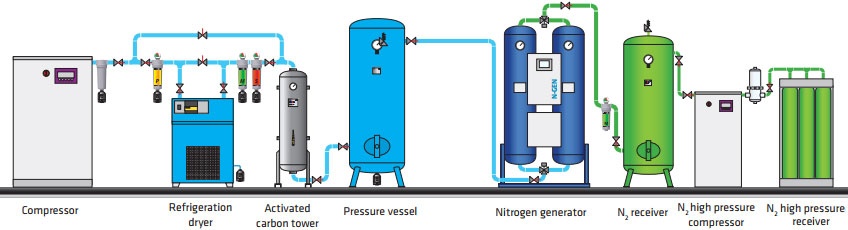