An overheated air compressor is the effect of internal issues, external settings, or some cases both. At particular moments in the system cycle, the air turns hot due to the procedures entailed, though it quickly cools before it gets to the endpoint. Nonetheless, if the air becomes too hot for the compressor to handle, something is incorrect with the machines and their equipment.
Causes of Air Compressor Overheating
In many cases, overheating is a comparatively common problem that affects the air compressors’ regular performances; the risky heat experienced during the summertime can wreak even greater havoc on your compressed air system – or intensify already-existing issues.
Internal and external factors can affect the air compressor unit, and typically the air will become hot before it cools and reaches its endpoint. Thus, ventilation of the air compressor is crucial to ensure it’s running.
For the air compressor’s best performance, the temperature at the discharge line should never exceed around 107 ⁰C. Anything warmer at the discharge line would put the discharge port dangerously above the 148 degrees Celsius level. If the temperature exceeds 176 ⁰C in the discharge port, the heat could lead to imminent system failure.
Accomplishment to this significant problem of what is causing the compressor to overheat is a challenging task. Some common reasons for overheating situations are –
- Less Maintenance – If the compressor does not experience periodic maintenance, then dirty, cracked filters, blockage on pipes, and some blocked internal components could lead to overheating problems.
- Old Compressor – An old-aged air compressor, undergoes excessive use of air compressors is more likely to cause overheating scenario.
- Insufficient ventilating system – The compressor system must have some self-capability to cool itself down, so if there is no proper ventilation available in the compressor room, overheating could result.
- Higher Ambient Room Temperature – Summer times make ambient conditions warmer. The outside hot weather, the more likely the compressor room is warmer. If the compressor room is too hot, the air compressor becomes overheated.
Main Reason behind Air Compressor Overheating
So right here, this article will certainly provide some instruction that will certainly aid in learning why the compressor intends to end up being a cooker (getting too hot) and also exactly how to remedy these problems.
One of the main reasons that can occur an air compressor to overheat is a high compression ratio, which is naturally caused by low suction pressure level. These circumstances that contribute to low suction include the following:
- Improperly close-fitting components
- Metering devices Fault
- Refrigerant loss
- Blocked strainers
- Abnormal Pressure drops
If there is any fault in metering devices, as an example, the ability to monitor the system with accurateness becomes compromised. To keep a high value of suction pressure, it is vital to check for signs of these issues regularly.
- Excess Discharge Pressure –
Air compressor overheating consequence of excess discharge pressure, which typically come from one or more of the listed categories –
- Dirt in condensing coils
- Ill-fitted discharge line
- Obstruction of condenser air
- Poor quality condenser fan
- Refrigerant overcharging
- Inconsistent condenser
For maintaining discharge pressure levels under control, one should check the condensing parts in a routine wise for signs of any problem issues. Even on larger systems with in-built discharge monitoring, issues can go undetected until the problem spreads to other parts of an air compressor.
A blocked oil cooler will certainly limit airflow that is likely to remain oil cooler at a reduced temperature level, ensure that the colder is clean as well as absolutely nothing limits the airflow.
- Motor for the fan cooler –
Check on the fan cooler to see if it’s working. if it’s not functioning, examine the fan cooler readying to know if it is disabled, examination voltage at the motor to locate if there is the accessibility of electricity, test the electric motor itself to see if its working condition.
The combination shutoff valve depends upon heat to open up as well as let oil flow to the oil colder. A malfunctioning combination valve indicates that warm oil will flow back to the air. Therefore, increasing the temperature. If it’s damaged, make sure to change with the newer pieces.
A blocked oil filter will undoubtedly deny the air end of oil to cool it at the time of air compressing. A clogged oil filter will also indeed provide an alarm system revealing oil filter adjustment in pressure and is rising.
A reduced oil level indicator indicates that the device does not have sufficient oil to cool itself effectively. Ensure to top up the oil till the right level
whether there is trouble with the screw themselves or irons inside it. Without any doubt, this will undoubtedly cause overheating, and the only option will certainly be to replace the entire air end. Check out exactly how to change an air end of an oil-injected rotary screw compressor.
Ensure that the compressor is installed in a place where there is abundant awesome airflow and also where the ambient temperature level is low. In the case of ducting, ensure ducting itself is not blocked.
Different applications demand different air compressors. If someone is working with heavy-duty machinery round the clock using a small air compressor, they are at high risk of overloading the machine’s actual capacity. In the same way, it is best to gauge the age of the existing compressor. If it is 20 years older, then it might be time for a replacement. When receiving an air compressor for any company, always consider its scope, size, and capacity with the demands at hand.
Older air compressor units and those that bear to high sunlight daily tend to suffer from insulation problems. Without appropriate and satisfactory insulation, the compressor will heat up frequently. When there is too much heat, the compressor may include breakdowns.
- High Voltage and Short Circuits –
At the time of occurring high voltage surge, there is likely for compressor difficulties to follow. Not only could the unit overheat, but it also trips the circuit. If the outside unit’s having trouble turning on and keeps tripping the circuit, ensure HVAC rechecking. A short-circuiting occurs rare for air compressors, but it can happen anytime
To overcome overheating of the air compressor, operating above the Ambient Design Point is a crucial challenge. Let’s have a discussion
Signs That Your Air Compressor Is Overheating
When any air compressor becomes very warm, it starts performing problematically. The likelihood is that it might be from overheating heating.
- Compressor Turning on Issues
If the compressor goes wrong to start up as standard conditions, there is certainly something incorrect with the machine that could likely come from an overheating heating issue. If the compressor takes more extended periods between its cycles, the internal parts are possibly taking a lengthier time to cool down among its processes. Similarly, if the compressors stand stop during arrangement for starting and eventually take a longer time to get into complete operational mode, this is undoubtedly due to heat-degraded internal setup.
- Tripping the Circuit Breaker
In the air compressor system, the electric power is controlled by using a circuit breaker. This safety instrument stops the electricity flow depending on the compressors’ performances. If the circuit breaker functions wrong and trips the circuit breaker, this is a sign that more significant problems lurk inside the compressor.
At a time when an air compressor jumps to wear down at a faster pace, there is possibly a thoughtful matter approaching. For instance, if the compressors show issues on the performance just a few times after it was last checked. Something was perhaps not assessed correctly; there can be something wrong in the oil, ventilations, the condenser mechanism. If the air compressor is extended before its time and so far, failing to meet immediate demands and requirements, there could easily be a problem related to overheating.
Normally, air compressors emit some noises and smells representing oil leakages. If there are any dim creaking noises from the compressor’s machine that look generic. it might be an issue of lacking a lubricated internal mechanism. A more key indicator of oil-related problems is when an air compressor smells of burnt oil frequently. Either way, the matter must be reviewed instantly, as inadequate lubrication and bad oil quality can occur a domino effect on the internal parts.
How to Prevent Your Air Compressor from Overheating Problem
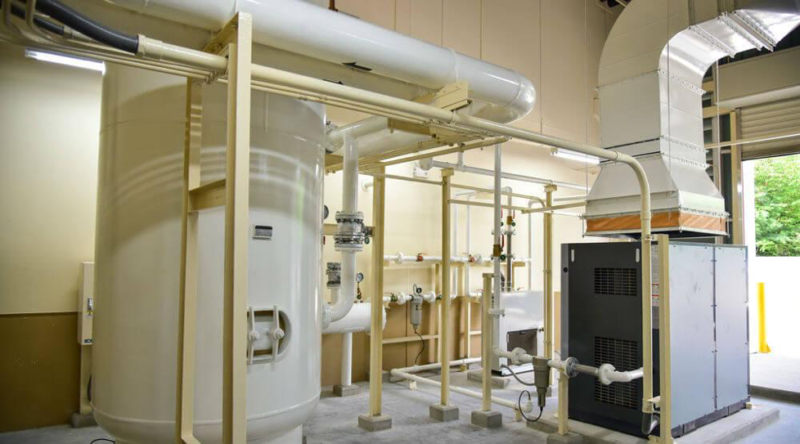
If you want to cool your air compressor down and work to prevent it from overheating. Here’s what you can do:
- Improve Ventilation System
The initial step toward reversing a heating issue with an air compressor should focus on the internal and surrounding ventilation accurately. Check each vent to ensure that they are enough for the demands of the machine. If not, then it’ll need the vents replaced without any delay.
Also, concentrate on the external factors of the machine itself. If the engine is installed in an area that is either very hot or not ventilated sufficiently. Arrange some space for the device in a more appropriate place. Ensure that this new settlement lets sufficiently breathing room for each and every vent.
- Monitor the Oil Level and Filters Regularly –
In any motorized machine, it is vital to make sure the oil of the air compressor is in good condition. Examine the oil level frequently to ensure that there is enough oil to handle the demands of required operations. As well, check the viscosity to ensure that the oil has not been reduced to thinner or watery. This would be a symbol of excess heat within the air compressor’s system. Additionally, monitor the filters during each oil checkup time.
- Monitor Ventilation and Ducting –
After modified the arrangement of the workspace to healthier ventilate the air compressor and the surrounding temperatures. Check the ventilation and ducting frequently. If there is some dirt or dust accumulated along with the vents, clean them out properly. Ensure that the ducting flows accurately and is not crimped or punctured at any point of the system.
Even if, in all practicality, you found no reason to reposition the machine, the vents could still have issues if they don’t receive due attention. An air compressor that cannot correctly vent is liable to have heating issues, regardless of where the machine is placed.
- Keep the Compressor Parts Up-To-Date –
Any air compressor that you bought last year might not be sufficient in its original state as the demands of operations grow. If your operations have demanded increased amounts of airpower since the time that you first bought the machine, consider updating your air compressor with more optimal components.
Always check and clean your machine. Schedule a time and date when to conduct it so that you will not disrupt your facility’s operation. Hire a reliable and licensed service provider to inspect your air compressor and perform any necessary adjustments periodically. They can also provide you with advice on how to best use the machine to avoid any complications in the future.
If a thermal valve starts to fail, overheating can occur. It is always advised to keep a spare thermal valve on hand in case of an emergency and to avoid any downtime for your business. The spare valve can also be used for comparison to see if your current valve is in good working shape or if it needs to be replaced as a preventative maintenance measure.
The most frequent reason for an overheating air compressor is the surrounding hot temperature and warmer environment that it is in. Make arrangements for keeping the air compressor near to direct sunlight in the middle of summer. Avoid keeping any hot equipment next to the compressors. Build a proper insulation system in case of small space. All of these setups are preventable issues to retain a lower temperature in the surrounding environment. Try to keep the air compressor away from windows, especially in hot climates, and do not let the air compressor sit next to other operational equipment that can become very hot.
Operating the Air Compressor over the Ambient Point Level
The potential influence on rotating screw air compressors operating above their ambient design factor is that it might reduce the life of the electric motors or cause them to fail in working. Operating any type of electrical motor over its thermal design will likely cause the windings failure. The grease used on the primary engines is made for a certain optimum ambient temperature level. Running over that design point will need re-greasing in a lot more frequent periods or an optimal grease to handle the warm build-up to stay far from winding or bearing failure. Making use of a non-OEM oil may not cool the air compressor correctly. This will trigger the air compressor to operate at a raised internal temperature and also, with time, bring about failing. This can also cause inner varnishing of the air end.
A good correlation of varnishing in an air compressor resembles plaque building upon its teeth. Non-OEM oil will trigger accumulation on the orifices, rotor/stator clearances, rotors, etc. This can reduce the life of the air end as well as cause an early re-build or substitute. This implies possibly facing along as well as unexpected closure with unanticipated maintenance expenses.
An air compressor space with precise airflow offers fantastic air for the inlet of the air compressor. It likewise consists of ducting to take the discharge warmth out of the area.