Improper piping can lead to many problems, including inefficient air flow and energy loss. Therefore, it is essential to know how air compressor pipes work.
These pipes simply transport compressed air in-and-out of the compressor. However, they must be selected according to the system design. Their construction, size, and durability are highly important.
This guide explores the main selection criteria for air compressor pipes. Before purchasing, all compressor system owners must consider these factors. Otherwise, they risk increasing energy and maintenance costs.
Here are the main factors:
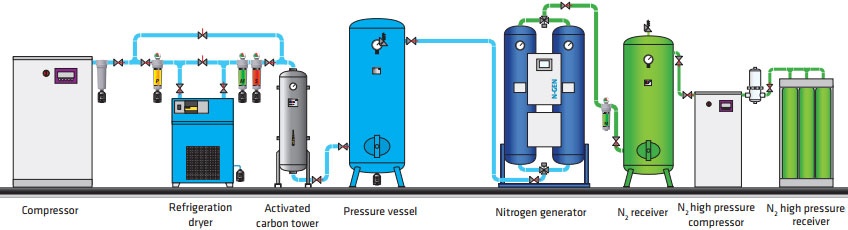
Different Types of Piping Materials
Firstly, it is essential to evaluate the different types of piping materials. Piping materials determine the long-term performance and durability of the entire air compressor system.
Overall, there are two main types of piping materials:
Plastic
Plastic piping is most desirable for its cost-effectiveness. Due to its lightweight and malleability, it is easily installable and long-lasting. In all industrial fields, there are two categories of plastic piping: PVC/CPVC and ABS/PE.
The former stands for (Chlorinated) polyvinyl chloride, which is a synthetic thermoplastic. It is not a good option for compression systems because it cannot withstand high-pressure air distribution. Most OEM sector companies use these pipes for plumbing and construction.
PVC/CPVC pipes are cheaper and easier to install than other plastic pipes. However, they are not ideal for air compressors.
It is essential to evaluate the plastic’s longevity and exposure to corrosive substances. For example, if a plastic pipe is exposed to lubricants, it can damage the structural integrity. This is very common in PVC/CPVC pipes.
Most air compressor systems last for years if not decades. Therefore, the plastic piping must be able to endure long-term usage.
The latter category, ABS/PE, is ideal for this reason. ABS stands for acrylonitrile butadiene styrene whereas PE stands for polyethylene. HDPE is high-density polyethylene.
Both ABS and PE pipes are lightweight and non-corrosive. Installers may cut the pipe to fixate it in place. Moreover, both the internal and external surfaces are smooth, creating more efficient air flow.
Metal
However, regardless of material quality, plastic pipes always have some limitations. Metal pipes, the second category, are more desirable because they can withstand higher-level air pressure for years. Moreover, metal pipes limit risks of air leaks.
For air compressors, the most common metal piping materials include iron and steel. Black iron pipes offer the best performance in the market. They can last decades and are easily welded to different parts. However, they are quite expensive.
Steel pipes come in two categories: galvanized and stainless. Galvanized steel pipes are very similar to black iron pipes. However, the added galvanization makes the steel less prone to corrosion.
Stainless steel pipes are even more resistant to corrosion. According to industry experts, they are the longest-lasting pipes, particularly for air compressor systems. Their only drawback is their lack of malleability; they are difficult to cut and costly to install.
Aluminum and copper are two cost-effective alternatives. Aluminum pipes offer high resistance to corrosion, leaks, and breakage. At the same time, these pipes are lightweight, making them easier to install.
Unlike iron or steel pipes, aluminum alternatives do not need added support. If they are being installed on the ceilings, they can be fitted and modified without specialized equipment.
Copper pipes are cross between steel and aluminum pipes. However, their high cost makes them undesirable.
Compressed Air Pipe Sizing
Apart from the material, size is another vital factor for selecting air compressor pipes. Choosing the wrong size can either rupture the pipe due to over-pressurization or cause energy loss due to under-pressurization.
When selecting the pipe size, consider the following factors:
CFM Requirements
CFM stands for cubic feet per minute. It is a unit of measurement representing how fast air flows through the pipe i.e. how much distance it covers in a minute. Most air compressor systems come with CFM ratings.
However, if it is not specified, the CFM rating of a particular compressor system is easily available online.
Users may contact the manufacturer or consult authority pages such as expert blogs or articles. The former is preferable because manufacturers have more accurate information regarding a specific system.
Expert pages, no matter how reliable, may display CFM charts, which may be inconsistent with the requirements of a particular system.
Overall, it is important to look at the maximum CFM value as it will indicate the maximum distance the machine can cover in a minute.
Minimum Operating Pressure
Pipe size also depends on the compressor’s minimum operating pressure. Taking this into account ensures no pressure is lost between two connecting pipes. It ensures the pipes distribute air evenly.
Luckily, this value requires no calculations or research on the user’s part. The value is always specified by the manufacturer either on the product website, in the specifications, or in the user manual.
The value is measured in psi (pounds per square inch).
Location
Sizing depends also on the installation location of the air compressor system. Usually, large-scale air compressor systems are installed in industrial locations. If the pipes are being installed in the ceiling, their length and width must match accordingly.
Of course, various types of fittings aid the installation. For example, male and female elbows and connectors are common fitting tools.
Such tools help secure the pipe according to the size of the location. This is especially true if the pipes are metal and require support to be propped up.
Such fittings are widely available in different materials. However, it is essential to match the fitting material to the piping material. Do not buy nylon or synthetic fittings for metal pipes and vice versa.
Fittings can make up for any gaps between pipes, acting as connectors. However, sizing the pipes according to the location often requires modifications.
Therefore, it is better to purchase pipes larger than the actual location size. This leaves room for cutting, welding, and other shape changes.
Application
Lastly, the intended application should also be factored into the sizing decision. Depending on the application, the pipes need to be either powerful or mobile. In terms of sizing, this means the pipes should withstand certain pressure settings or should be light and easy to carry around.
For example, painting with a pneumatic brush requires air compressor pressure. However, the pipes need to be small and agile, allowing swift brush movements. Therefore, half-pipes are preferable for this application.
Considering the Pressure Drop Levels
As mentioned, pressure correlates with sizing in different ways. Consequently, pressure drop levels are a key consideration and require further deliberation.
What does pressure drop mean exactly? Pressure drop refers to the pressure loss between the compressor machine and the air output.
Regardless of the type and quality, air compressor systems always have a pressure drop. This is not necessarily an undesirable quality. Pressure drop levels indicate how much control the user has over the machine.
Most air compressor systems have a peak pressure point of 95 psi. This means the operating pressure, as mentioned above, will be 98 psi. Here, the pressure drop level is 3 psi because that is the difference between the two values.
However, excessive pressure dropping is undesirable. Air compressor systems usually drop pressure when the airflow loses traction in the pipes.
This happens when a pipe is under-sized, meaning it is small in length yet longer than it needs to be. The air cannot flow properly, resulting in a drop of pressure. Therefore, it is better to make the pipes as short and wide as possible.
Usually, oversized pipes do not impact pressure. However, they are costly, making them a futile investment. The only reason to obtain oversized pipes is aesthetics. However, they have no functional value.
How to Layout the Compressor System?
Once the pipes are purchased, the next step is to modify them according to their installation space. Several factors affect the positioning of the air compressor system.
For example, the layout should minimize sharp angles. Although fittings such as unions and connectors prevent leakage, they can also reduce efficiency.
Therefore, use fittings as minimally as possible, avoiding sharp angles in particular. Sharp angles require the air to bend, which substantially reduces pressure levels.
Similarly, avoid installing the pipes in a moisture-prone area. Both plastic and metal pipes respond badly to moisture. Plastic pipes are less corrosive. However, consistent exposure to moisture may impact their structural integrity.
Metal pipes, particularly iron and steel, are more corrosive. Exposure to moisture may cause them to rust and degrade. Consequently, the compressor system’s internal moisture should be properly regulated.
The compressor machine usually absorbs moisture from its in-let source, transferring it to the air in the pipes. Simply change the source when this happens. Moreover, use an after-cooler, which helps reduce air temperature and removes moisture after use.
To begin the pipe layout, installers may use one large pipe as a guide. Begin with a single, large-sized pipe, connecting it to the machine. From there, simply weld the other pipes and fittings to the main pipe one-by-one.
This method is called the ‘highway’ approach. It involves centering the layout to a ‘highway’ pipe, creating several sub-sections from that main pipe.
Another approach involves using a ring pipe as the central point. This pipe will connect all the subsections, surrounding them in a ring-like fashion.
All in all, it is not difficult to understand air compressor pipes. There are a few key considerations to evaluate when selecting the right pipes. However, the task is achievable with a bit of research and dedication.
As mentioned, air compressor pipes are a fundamental part of the compressor system. Although the compressor machine is the crux of the system, it is futile without the correct piping system.