There’s a lot more to it than meets the eye though, so below we’ll walk through the differences between these two compressor types and discuss their benefits and drawbacks.
Direct Drive Air Compressor
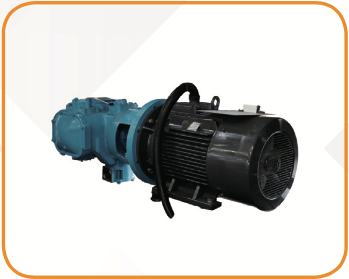
What is a Direct Drive Air Compressor?
A direct drive air compressor is an air compressor that uses the motor as a rotating shaft. This means there’s no belt or pulley system, which makes them smaller and lighter than their belt-driven counterparts.
These are generally more common in small, portable compressors with less power output.
Working principle of Direct Drive air compressor
The working principle of a direct drive air compressor is very simple. As the motor turns, it rotates two or more gears that in turn spin an even smaller gear inside the cylinder which compresses the gas into liquid form.
The piston and crankshaft assembly are also connected so they move together as one unit without any type of belt or pulley to get in the way.
Advantages of direct drive air compressor
The biggest advantage of a direct drive system is that it’s compact and lightweight, which makes it very portable for on-site applications. It also doesn’t have any belts or gears exposed so you won’t need to worry about replacing them as often.
Disadvantages of direct drive air compressor
The biggest disadvantage to a direct drive system is the lack of power. Since this style uses the motor itself as the rotating shaft, it can’t produce anywhere near as much power as belt-driven compressors that use larger gears and belts. This makes them less efficient for heavier-duty applications such as powering tools and equipment.
Belt Drive Air Compressor
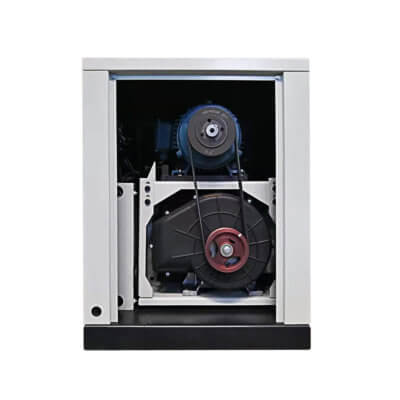
What is a Belt Drive Air Compressor?
A belt-driven system uses an engine and crankshaft to turn a pulley that in turn rotates the center shaft inside the cylinder where two or more gears are attached for compression.
This type of style has been used since the beginning of air compressors, and while they are slightly heavier than direct drive systems, these have greater power output.
Working principle of belt drive air compressor
The working principle behind a belt-driven system is very simple: as engine speed increases so do cylinder compression speeds which ultimately result in more airflow and therefore higher pressure.
The key to this type of system is the pulley and belt assembly that connects the crankshaft with a center shaft inside the cylinder. The gears attached to these two pieces drive rotation which in turn drives compression.
Advantages of belt drive air compressor
The biggest advantage to using a belt-driven style is power output: since there are larger gears and belts, these systems have greater power than direct drive air compressors.
They are also more efficient for heavier duty applications thanks to their large size and ability to maintain high pressures even when the engine is under heavy loads.
Disadvantages of belt drive air compressor
Since this style requires a larger motor with exposed components that may require more frequent maintenance, belt-driven systems aren’t as portable or lightweight.
These also require more space due to their larger size and weight which makes them less ideal for applications where you’re working in tight areas with limited floor space.
Differen between direct drive and belt drive air compressor
Efficiency:
Belt-driven systems produce more pressure and airflow than direct drive air compressors.
Power:
Belt-driven air compressors have greater power output thanks to larger gears and belts that allow them to maintain higher pressures even under heavy loads while the engine is on/off or running at idle speeds.
Portability:
Direct drive style is smaller, lighter, and has fewer moving parts which make them ideal for on-site applications.
Size:
Belt-driven systems are slightly larger and heavier than direct drive air compressors, but these aren’t as bulky or heavy-duty since they’re better suited to lighter duty work with fewer components that may need more frequent maintenance.
Price:
Direct drive systems tend to be cheaper since they require fewer parts and are smaller overall.
Maintenance:
Direct drive systems tend to need more frequent maintenance due to their lack of belts or gears that may be exposed, but this increases the power output even further.
Belt-driven air compressors have larger components which means they are better suited for heavier duty applications, but these do require more frequent maintenance.
Sound:
Belt-driven compressors are quieter than direct-drive systems since there is no extra noise from the motor itself which means that these units can be used for long periods without causing excess fatigue or discomfort.
Oil loss:
Belt-driven systems have less overall oil loss which makes them ideal for applications that may be exposed to a variety of contaminants or dirty environments.
Application:
A direct drive air compressor is better suited to smaller, lighter duty work where there is limited floor space and tools need more frequent maintenance.
Belt-driven compressors are larger and designed with heavier duty applications in mind thanks to their increased power output and less frequent maintenance.
Ease of use:
A direct drive air compressor is easier to transport since they’re smaller, lighter weight, and have fewer components that may cause issues during the work process.
Belt-driven systems can be a bit bulky for onsite applications where there is limited floor space which makes them less ideal for applications where you’re working in tight areas and are more likely to be used at a shop or facility.
Does it matter which one I choose?
Both direct drive belt-driven air compressors have their pros and cons, so the best option depends on your needs. If you need an efficient and powerful unit that is easier to transport and has fewer moving parts, then the direct drive system will be best suited for your needs.
If you need a larger air compressor with increased power output thanks to more gears or belts which require less frequent maintenance, then belt-driven systems are better suited for onsite applications where there’s little floor space available or tools that need more maintenance.
Both direct drive vs belt driven air compressors are more efficient, powerful, portable and lightweight than other types of compressors. But each style has its unique pros and cons that make them ideal for different applications so it’s important to consider your needs when choosing the best unit for you.