This is most likely due to a Pressure Drop.
It is one of the common problems. It may take a length of time to pinpoint the exact cause within the machine, which can cost you a significant amount of money.
This guide will try to cover ways to pinpoint the problem and minimize the screw air compressor’s pressure drop.
What Is Air Compressor Pressure Drop?
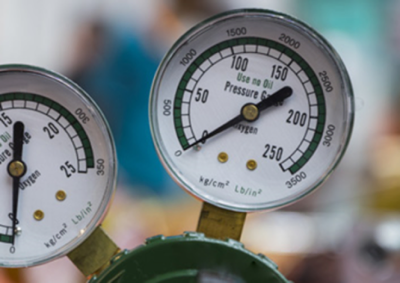
Pressure Drop is basically the difference between the pressure at the point of discharge and point of use. For instance, if the air compressor produces 120 PSI of pressure at the discharge point, but gives only 90 PSI at the point of use, then the difference of 30 PSI is the pressure drop.
How to Calculate Pressure Drop?
You can use the following “empirical formula” to calculate the pressure drop between the compressor and the point of use:
dp = 7.57*(q^1.85)(L)(10^4)) / ((d^5)*p)
The letters in the formula represent the following factors along with their measuring units:
- dp: The drop in pressure (kg/cm2).
- q: The volume flow of air (m3/min).
- L: The pipe length (meter (m)).
- d: The diameter of the inside of the pipe (millimeters (mm)).
- p: The total starting pressure (kg/cm2).
Note: This formula is based on simple compressor-to-pipe arrangements. It doesn’t consider the possibility of flow reduction within an air pipe, turbulence, and the possibility of bends along the piping of a compressor system.
What Causes Air Pressure Drop?
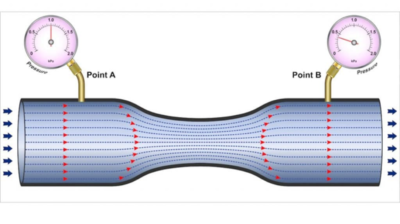
Primarily pressure drop is due to anything which hinders the flow of pressurized air. This can happen at various points between the air tank and the end-point tools of the air compressor.
Pressure drop also happens due to turbulence. It is created due to friction of air moving along the pipeline’s inner wall, which slows the air at the outside of the air stream, consequently causing the air in the middle to move faster.
Following are some of the common causes of Air Pressure Drop in Air Compressor:
- Undersized piping, dryers, and filtrations
- Extensive hose length
- Dirty or poorly maintained filters
- Excessive or incorrect use of quick coupling connections
- Incorrect piping configuration (for example: using dead-end piping instead of looped piping)
- Leakage in a hose that connects to a pneumatic airbrush
- High temperature in the surrounding
- Any physical obstruction, like gunk, along an air system
- Installation of Inappropriate component between the air compressor and the endpoint tools
- Using inefficient or low-quality air compressors
How Does Pressure Drop Cost You Money?
Pressure Drop can cost a significant amount of money in the form of energy consumption. To achieve the desired pressure at the point of use, operators usually try to increase the air compressor’s capacity, which leads to higher energy consumption.
For instance, the operator has to run the air compressor at 120 PSI to achieve 90 PSI at the point of use, wasting extra energy due to a 30 PSI pressure drop. As a rule of thumb, 1% of excess energy is consumed for every 2 PSI of over-pressurization.
It means if you have a screw air compressor with 125 horsepower, running on a 24/7 routine will cost you around $93000 per year in electricity to operate (at 10 cents per kWh). However, with 30 PSI of pressure drop (running the compressor at 120 PSI to achieve 90 PSI), the machine will cost $14400 extra due to a 15% increase in energy consumption.
How Can Pressure Drop Be Reduced?
You can’t eliminate the pressure drop. However, you can take several measures to reduce it. Following are some of the most effective ones:
- Check the pipeline and all the seals and connectors in your compressed air system for leakage. Change them if you see any cracks, bends, or leaks.
- Check and clean or replace the air filters and turn down the pressure set points on the compressor. It will help reduce the pressure drop and reduce the moisture that leads to pipe corrosion.
- Regularly inspect and maintain every component of your air compressor system. Repair or replace any faulty part.
- Monitor the pressure at numerous points of the system. You can measure the pressure between before and after points of each device attached to the compressed air system. Any unusual pressure drop should be addressed and fixed.
- Reorganize and reduce the unnecessary pipeline (hose) length by drawing a proper plan for your air compressor system. It would help if you also eliminate all the folds, bends, and leakage. Replace pipelines that are causing an unusual pressure drop.
- Replace your unreliable and low-quality air compressor with the reliable one.
- Use the after-cooler, dryers, filters, and separators for your compressed air system, which can effectively minimize the pressure drop during high temperatures, and peak operation.
- Determine and choose the pressure regulators, hose, and lubricators wisely to achieve the true flow rate instead of the average flow rate.
- Replace the tubes with cracks connected to the air compressor.
- Tighten or replace all the loose couplings in your system that can lead to leakage or pressure drop.
- Inspect and replace (if needed) the piping tees, valves, and nozzles for air leakage.
- Ensure that every connection point between pipes and other parts is air-tight sealed.
- Replace the old moisture separator with the new one if they fail to minimize the air’s moisture that passes through the compressed air system.
Hunting down the leading cause of pressure drop is a complicated process. So, it is highly recommended to undergo a professional inspection from trained and well-trained technicians. They will suggest to you what should be repaired and what should be replaced after proper inspection. Moreover, they also will commence accurate calculations for sizing the various components. It will save you time and money.